Efficient Distribution and Buffering of Material
Typical Problems in the Area of Automation
-
Production processes are to be automated in order to increase productivity. The aim is to ensure unmanned shifts or even unmanned weekends and to avoid machine downtime.
-
The customer requires to install a solution for counting produced parts, e.g. injection moulded, punched or die-cast parts, and to distribute them to different containers.
Buffering Systems for Improved Efficiency
MTF Technik has been involved in the automation of material flows in production plants for many years. Automated container management in particular (keyword: crate changer or parts buffering) is at the centre of this.
Different buffering systems are presented here, which can be designed according to the task at hand:
- Accumulation Tables
- Bunker Conveyor Belts
- Distribution Rockers
- Shifting Buffers
- Multi-Rounder Rotary Distributors
- Multi-Level Conveyor Belts
- Carousel Deposit Stations
- Conveyors as Linear Buffer
- Multi-Linea Buffer Stations
- Conveyor with Pneumatic Shifting Units
- Linear Buffer Conveyors
- Conveyor with Discharging Units
- Multi-Level Conveyors with Lift
Find out the best buffering system for your application using the enclosed checklist.
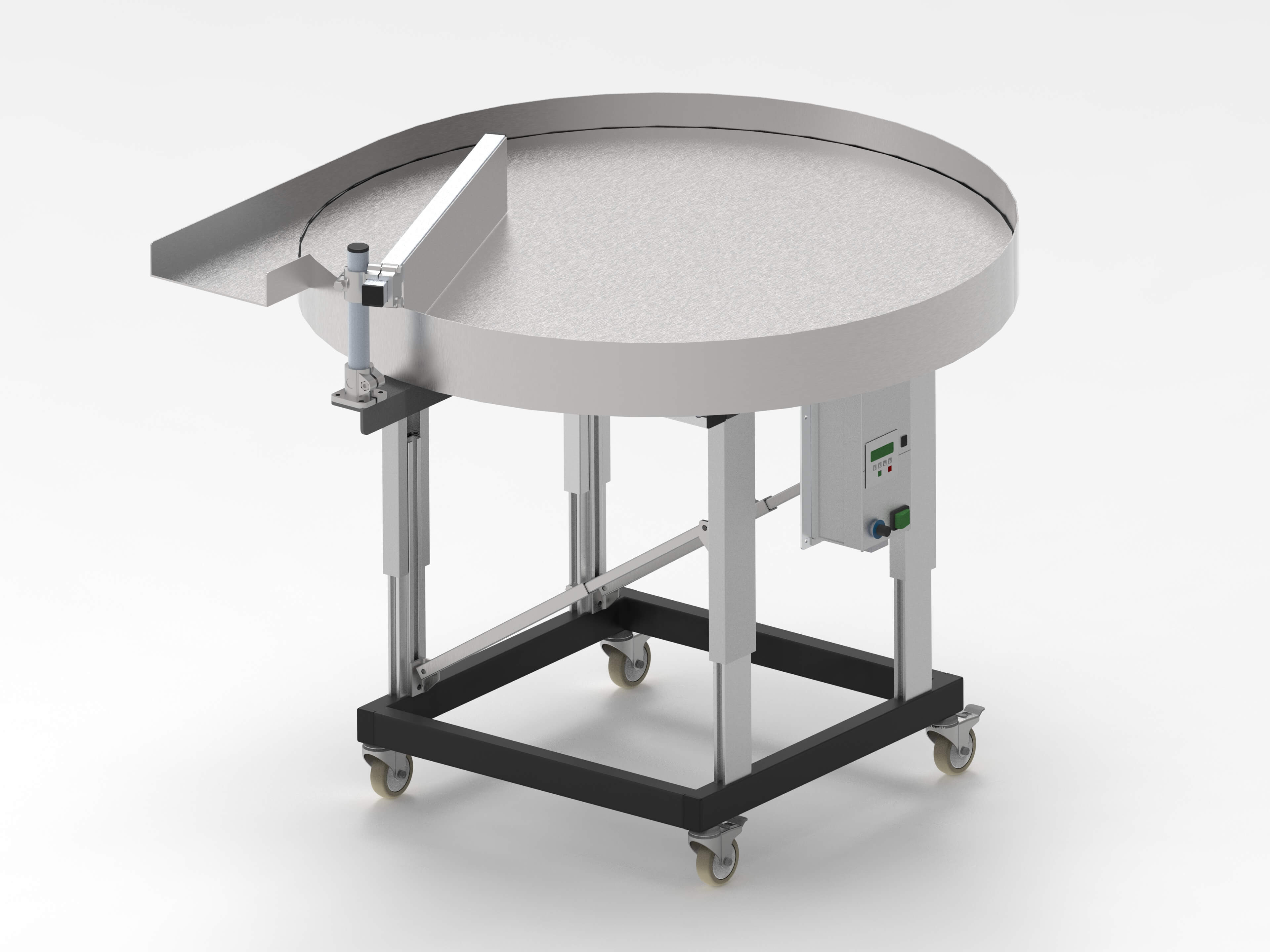
Accumulation Tables
Accumulation tables are used in particular for the short-term intermediate storage of individual products and are often located at the end of production lines where the parts are subsequently packed or handled manually.
These buffer systems consist of a round turntable, which is enclosed by a fixed side guide. The turntable is driven by an electric motor and rotates clockwise or anti-clockwise, depending on the application. Depending on the product and task, the turntable is made of stainless steel or plastic, while the side guide is usually made of stainless steel.
The rotary motion prevents product piles from forming or parts from falling on top of each other and possibly damaging each other. The products are transported in a circle and can be partially guided, fed in and/or discharged in a targeted manner using appropriate scrapers or guides.
Rotationally symmetrical parts (e.g. after a lathe in metal processing) can be accumulated and separated on these rotary tables in order to feed them to a subsequent process. Here, the rotary tables are used as short-term buffers, for example, to bridge different cycle times of interlinked work steps.
Due to their rather small size, they are usually equipped with a mobile base frame and can therefore be used flexibly at different locations. Depending on the product geometry, compliance with the FIFO principle can even be realised by using appropriate spirals on the accumulation tables.
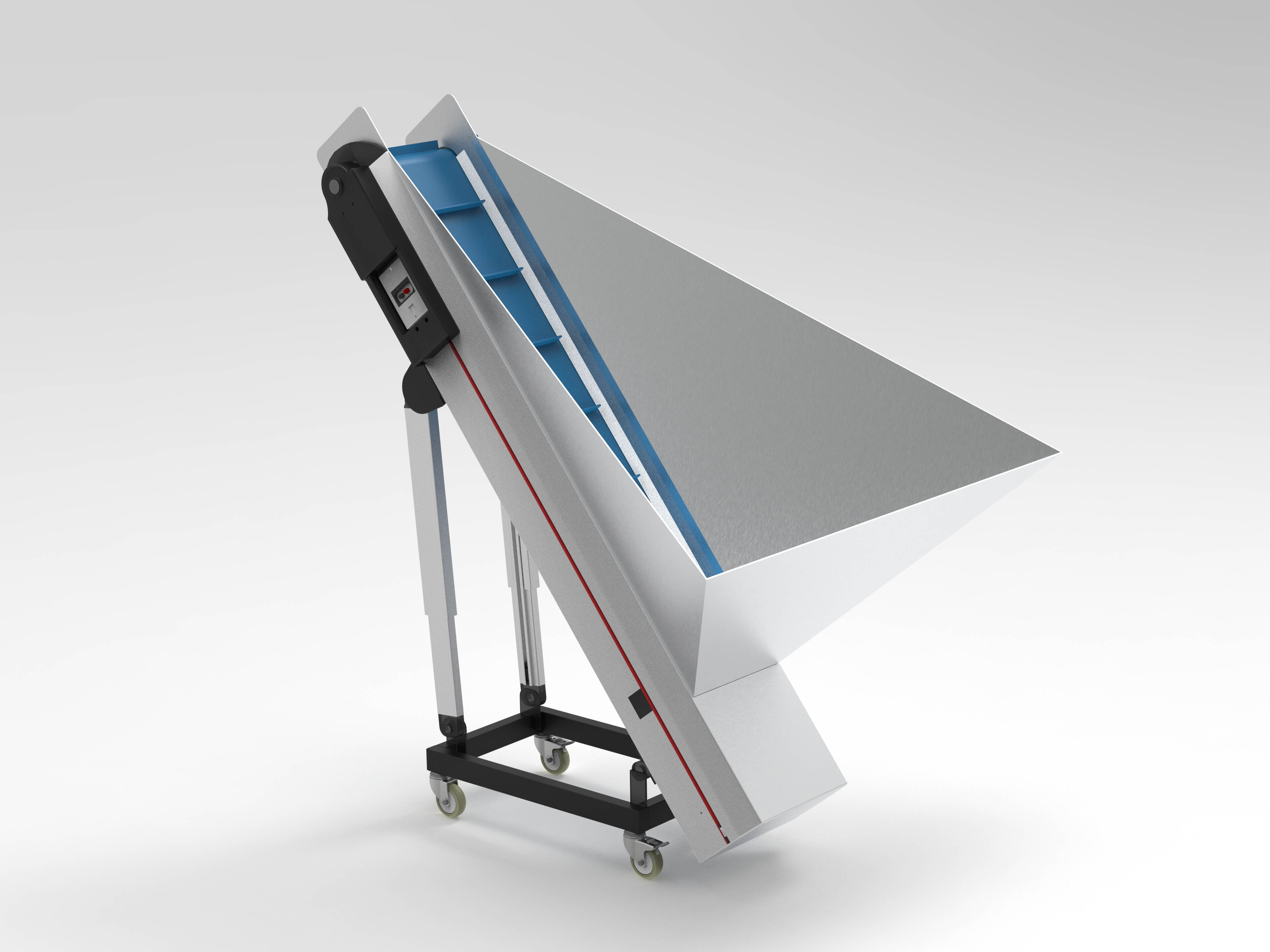
Bunker Conveyor Belts
Bunker conveyor belts are suitable for the short-term storage of bulk goods, as well. These are usually belt conveyors or steel hinged plate conveyors that are equipped with a large feed hopper. The hopper volume is then designed according to the part geometry and task. Hoppers with a volume of up to approx. 1.5m3 are not uncommon.
Such dosing conveyor belts are primarily used to feed material into subsequent processes. They are often used, for example, to fill vibrating bowls on assembly systems or to feed separating drums in a centralised separating task.
As a rule, either speed-controlled or intermittent drives are used to enable metered feeding. Depending on the task, feeding systems in combination with fill level sensors can also be realised in a relatively simple way.
When designing the hoppers for the hopper conveyors, careful attention must be paid to the part geometry in order to avoid any jamming or bridging processes.
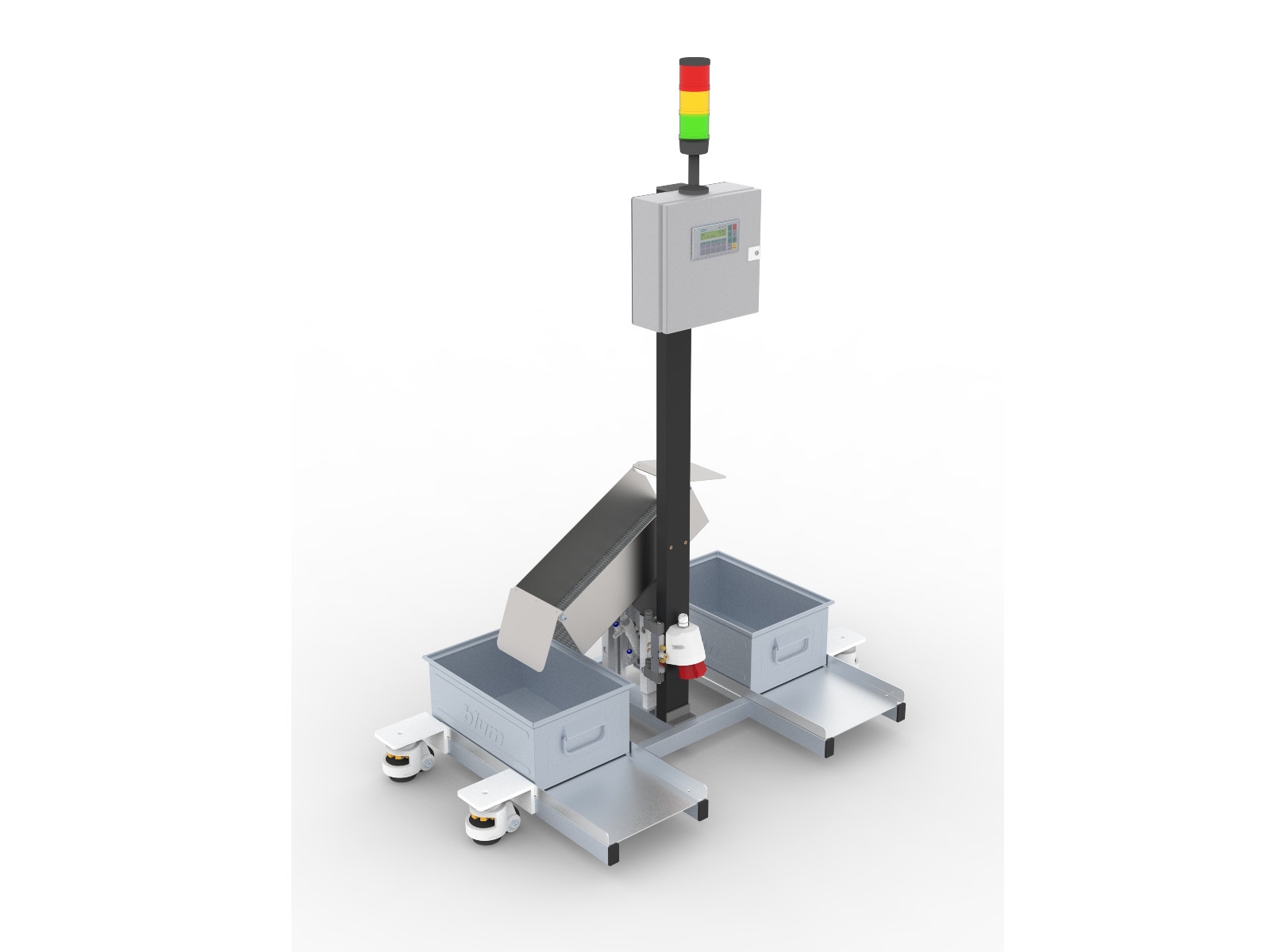
Distribution Rockers
Distributor rockers are usually pneumatically operated chutes that can be tilted into two positions and thus guide bulk material flows in two directions. Depending on the task, such rockers can be attached directly to the outlet of a conveyor belt or a separating device, for example, or mounted on a separate frame.
These distribution systems are primarily used where there is little space available or where distribution to two containers is sufficient. For example, two containers can be set up and filled directly next to each other. This optimises space utilisation.
Due to the simple design, the control functions required are also relatively low. In the simplest case, a 24V signal is sufficient to switch a spring-loaded pneumatic valve. Of course, end positions, etc. can also be queried - but this would require a more complex control system.
2-position distributor rockers are therefore a very favourable and space-saving option for filling two containers in order to create a small buffer system.
As an option, MTF Technik also offers distribution chutes that can take up two or even three positions. These chutes are similar to the distributor rockers, but they are in a closed housing and can therefore protect the flow of parts.
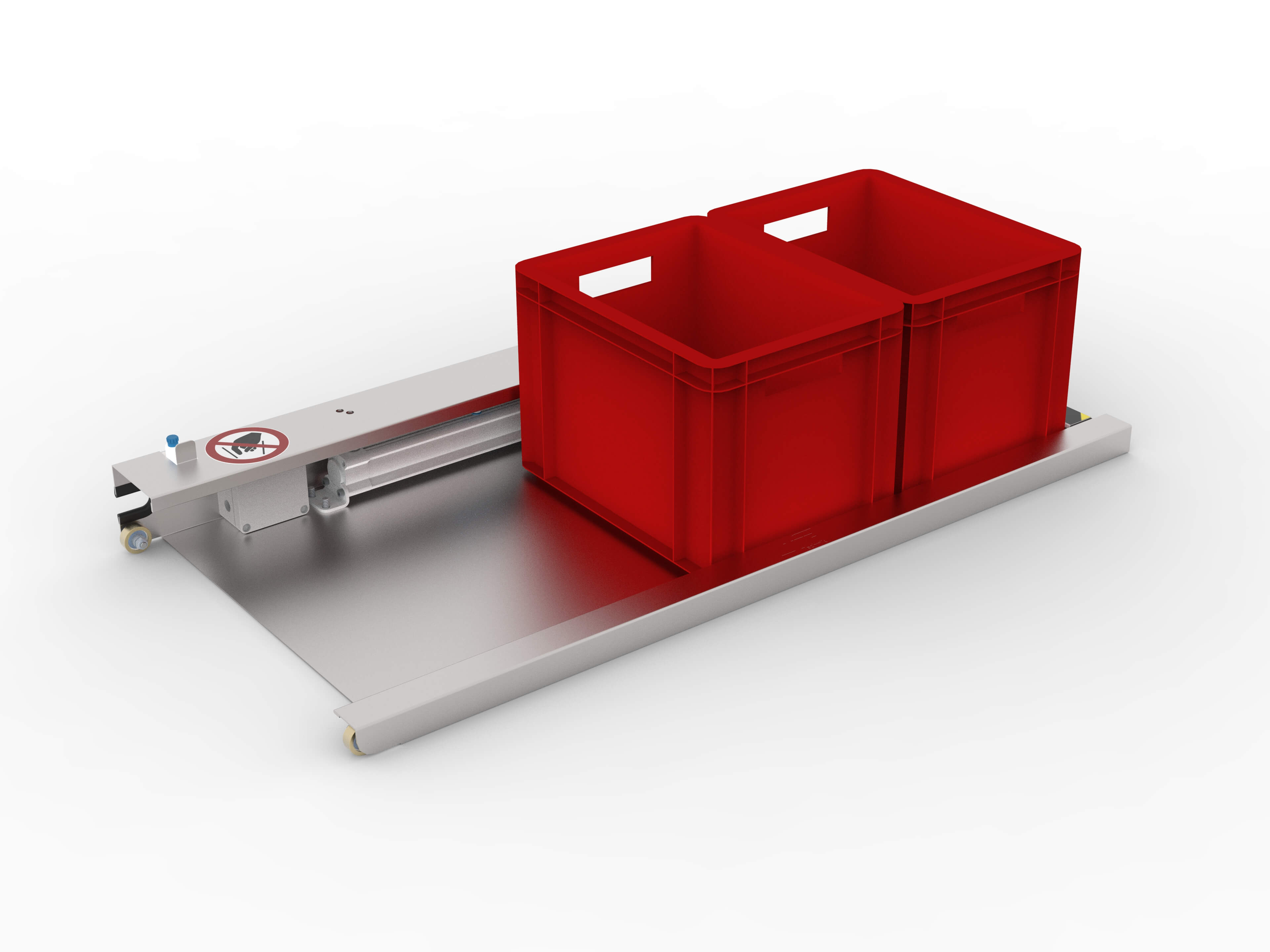
Shifting Buffers
The basic version of the sliding buffer consists of a stainless steel sheet base body with an integrated pneumatic sliding mechanism. Two to usually a maximum of three empty containers are placed on the base body, which are then pushed forward by means of a sliding arm in order to realise a container change.
In the simplest version, no additional control system is required for this; instead, a 24V signal can be sent from an existing machine control system to a spring-loaded pneumatic valve, for example, which only needs to be activated for as long as is necessary to move a container. However, for more complex tasks with more than two containers or intermediate positions - e.g. to avoid dumping cones - a more complex control system must be used.
The main advantage of the sliding buffers is their minimal height. The containers stand virtually directly on the floor, supported only by the sheet metal base, which is only a few millimetres higher. This makes these buffers particularly suitable for tasks where parts are fed in via low chutes or machine chutes, for example.
The sliding buffers are extremely low-maintenance, simple and comparatively inexpensive. They are the ideal solution for realising low filling heights and require little space.
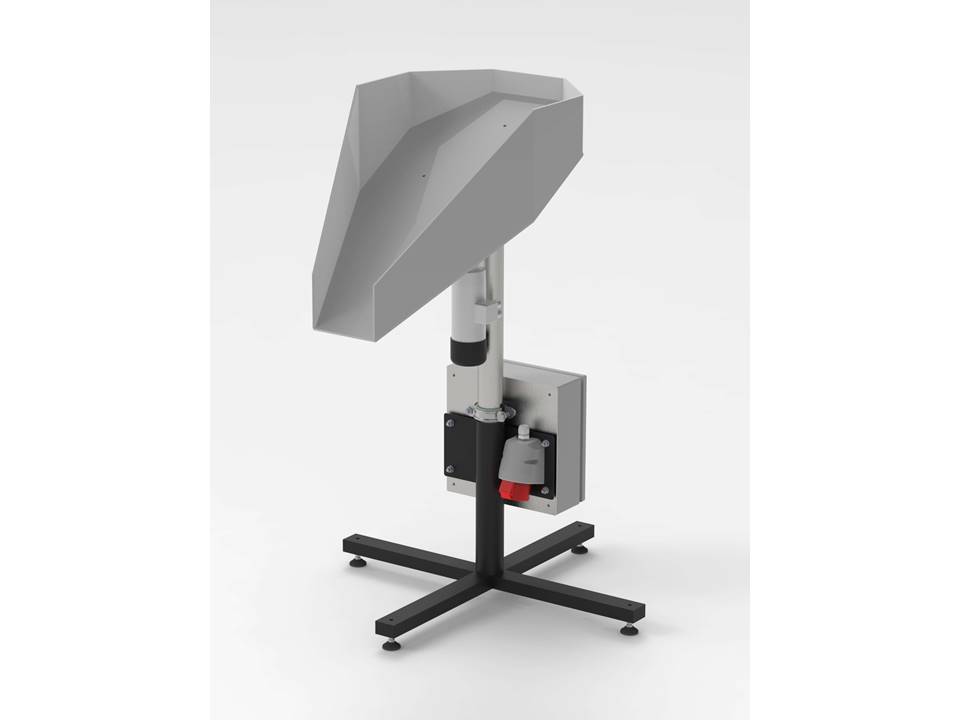
Multi Rounder Rotary Distributors
The rotary or swivelling distributor named "Multi-Rounder" is equipped with a chute that is mounted on a three-phase motor with a brake. The parts slide down the chute into various containers, which are arranged in a circle around the centre of rotation.
Depending on the design, the rotary distributor can perform complete rotations or alternatively swivel back and forth. This depends primarily on the filling position and the available space or any interfering edges.
The Multi-Rounder can be mounted below the outlet of a conveyor belt or on a separate base frame. Depending on the design of the base frame, container centring, container queries, etc. can also be provided.
The use of a rotary distributor usually requires a separate control unit that can analyse the positions and control the drive accordingly. The stop positions can be easily defined on the device using cams, as they can be added, moved or removed. This makes it easy to realise intermediate positions, for example, in order to avoid cones (several positions within one container).
Depending on the version, the device can be designed to be mobile so that it can easily be used at different locations.
The Multi-Rounders are generally used where - depending on the arrangement - up to a maximum of 6 containers are filled, but it is also possible to fill four pallet cages, for example. The ability to move to several positions in one container gives the multi-rounder a decisive advantage over distribution rocker or diverter units, which usually only have one discharge point per container and therefore create larger dumping cones.

Multi-Level Conveyor Belts
Multi-level conveyor belts are generally used as a multi-layer storage area for individual parts. In most cases, this involves short-term buffering of small load carriers at a production plant, e.g. where components are deposited by a robot and transported out of a safety fence. The conveyor belts are usually installed offset one above the other at the belt infeed in order to provide storage areas for crates at all levels, which can be reached from above by a robot.
These conveyor belts often serve to decouple the production process from a manual process, i.e. an operator removes the components from the delivery side. For example, a level can be completely filled over a longer period of time and the operator then clears the conveyor belt in correspondingly longer cycles.
The conveyor belts are customised in terms of length, width and number of levels depending on the task and desired buffer period. Depending on the existing control technology on the production system, the multi-level conveyor belts can be equipped with different electrical interfaces.
The advantage of the multi-level conveyor belts is that the components can be deposited in a defined manner and transported as piece goods. This is gentle on parts, prevents damage and can also be used very well for cooling processes, for example (also with additional fans or cooling equipment).
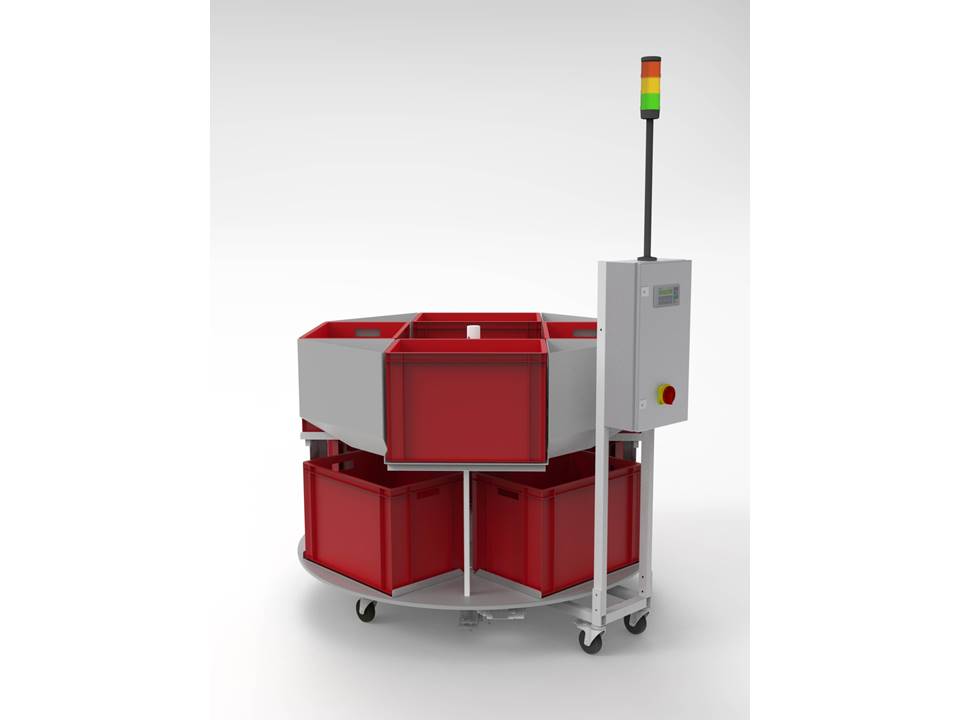
Carousel Deposit Stations
Carousel depot stations are pick-up systems that consist of a circular support plate as the basic unit, which is mounted on a stable ball bearing ring and rotates. The plate is driven from below by a three-phase motor with a friction wheel.
Boxes, cartons, small load carriers, etc. can be placed on the turntable and filled at a fixed transfer point. Cams are mounted underneath the base plate, which are scanned by a sensor and thus indicate the position. By attaching the cams accordingly, several stop positions can also be set up for each container if required in order to avoid cones.
As an alternative to the containers, bag holders or bag holders can also be attached to a rotating upper section. This allows the system to be used flexibly for different containers.
These pick-up systems are particularly space-efficient when containers are arranged in two levels on top of each other. For example, eight standard KLTs, each with a base area of 600 x 400 mm, can be accommodated on a turntable with a diameter of just 1,550 mm.
The advantage of these carousel buffers is that they are relatively inexpensive and very easy to set up. Maintenance costs are extremely low and reliability is very high due to the simple design. In addition, such systems can also be used very well in clean rooms, as they generate very little abrasion and all moving parts are located below the turntable.
Our carousel depot stations are individually constructed and designed for each application in order to adapt them to the customer's containers and the available space. They are usually used where a suitably circular installation site is available.
The basic controls of the pick-up systems can be set up very simply, as they only need to control one drive and one sensor. Depending on the task at hand, the control functions can of course also be significantly more complex.
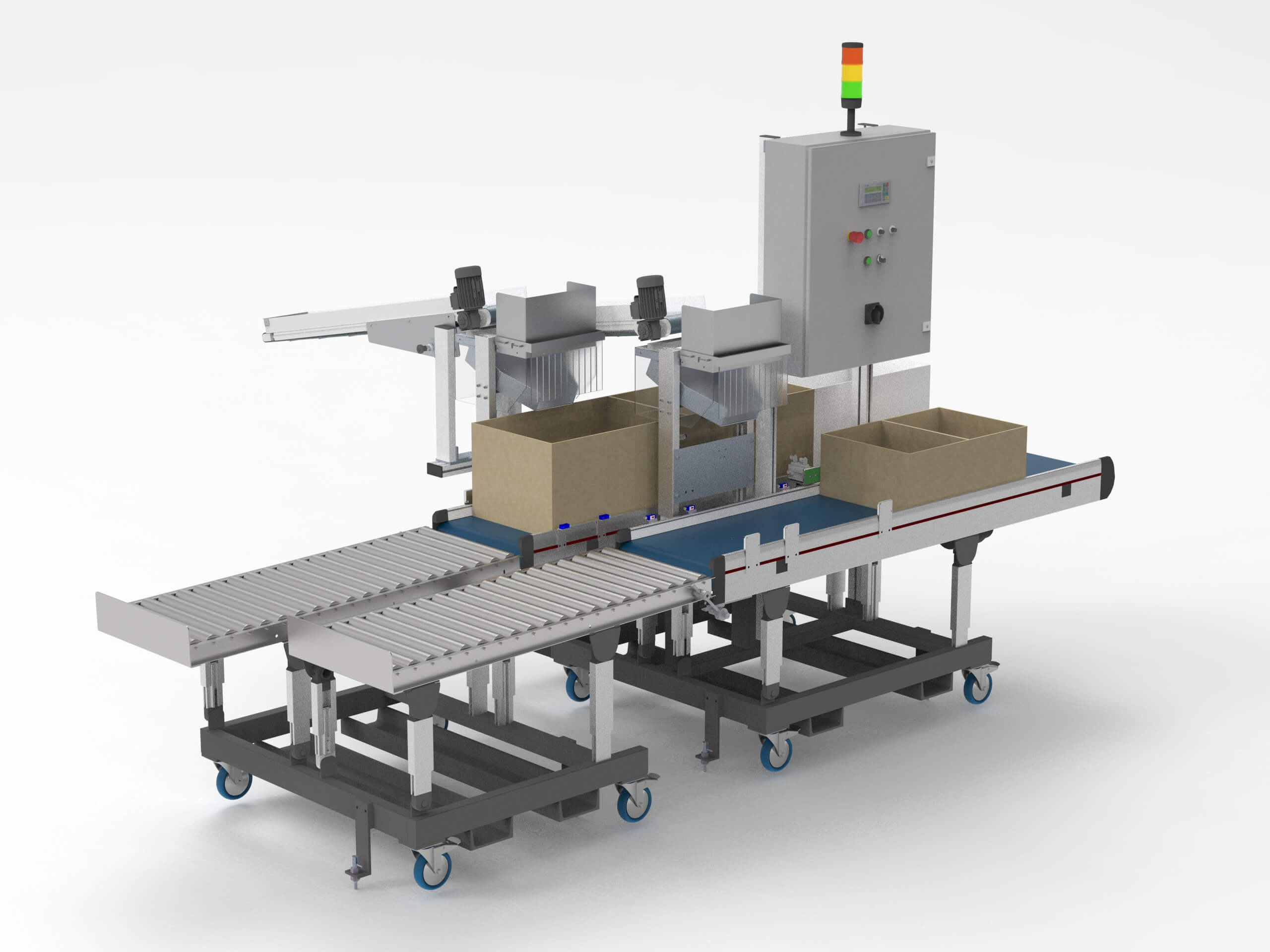
Conveyors as Linear Buffer
If production machines are positioned next to each other in parallel, for example, there is often very little space between the machines in terms of width for a buffer solution. In addition, there is usually the requirement that the machine must be accessible for set-up processes. In these cases, MTF Technik conveyor belts can often be used as linear buffers.
Several containers (cartons, boxes etc.) are placed on a conveyor belt, which are then moved to the respective filling position in a controlled manner. The cleats on the conveyor belt ensure that there is always a small gap between the containers, which can be easily monitored by a sensor. This means that each container can be clearly positioned at the filling position.
In more complex systems, pneumatic separating stations can also be used as an option in order to be able to move containers to the accumulation position. This is particularly important if, for example, different container sizes are used and fixed cleat compartments are therefore not suitable or containers are to be pre-accelerated into a protective fence to the filling position.
The linear buffers can be set up very flat so that feeding situations from low chutes are also possible. The disadvantage of these systems is the relatively large amount of space required, as the empty containers must first be stored and then buffered as full containers after the filling process. With a buffer solution for three containers, there must be space for at least five containers in total (the last container then remains in the filling position and the two already filled containers are pre-buffered in the two free spaces).
Optionally, the linear buffers can also be designed in two parts, i.e. the empty containers are fed to the filling station via a conveyor belt and the filled containers are removed via a roller conveyor. This is useful if, for example, filling takes place inside a safety fence or if, for space reasons, the filled containers can only be removed at the front discharge position. In this case, the combination with a roller conveyor offers the advantage that the removal of the filled containers can be realised independently of the feeding of the empty containers.
As the linear buffers can be designed to be mobile, they can be easily removed from the production machine if necessary, so that, for example, mould changes or similar are possible.
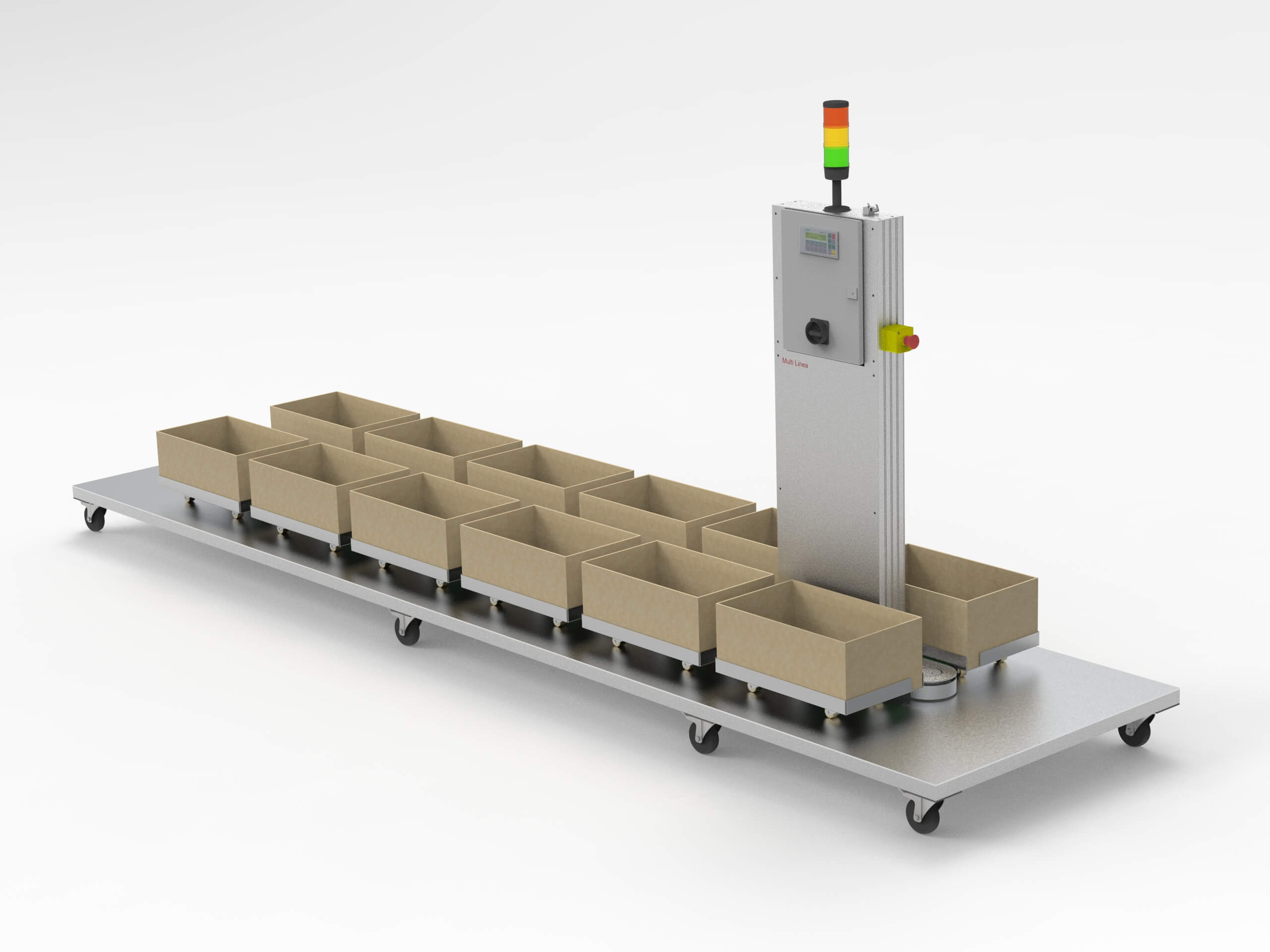
Multi-Linea Buffer Stations
The "Multi-Linea" is a circulating buffer in which containers, bags or sacks are placed on small mobile trolleys that are pulled by a chain drive. The container or bag holders are customised to the customer's requirements.
These circulating buffers are suitable if space is available along the length and the containers are to be positioned relatively low (e.g. because they are filled via a chute or similar). Due to the recirculating operation, all spaces can be used for buffering, i.e. the degree of space utilisation is high. The more containers are placed on the Multi-Linea, the better the utilisation of the area.
In order to avoid conical piles, the system can pre-clock sections of each container to ensure the most even filling possible.
In the basic version, the system can be equipped with a very simple control system, e.g. if it is already installed in a protective fence. For more complex projects, a Siemens S7 controller is usually used, which is individually programmed. This allows special interfaces, visual and acoustic signals, recipe management, etc. to be realised. The Multi-Linea systems can also be customised with regard to safety equipment or clean room designs.
The Multi-Linea is usually designed to be mobile and can therefore be used flexibly at different locations. The advantage is that each container can be changed flexibly during operation, as they stand individually on the mobile trolleys. This means that operators can remove filled containers and provide new, empty containers regardless of how full the Multi-Linea is. The system cycle does not have to be interrupted for this.
Standard multi-linea buffer systems usually have a capacity of between approx. 6 and 16 containers. The fewer containers are required, the more likely a carousel depot station is to be considered as an alternative, as these are cheaper and take up less space. With a larger number of bins, lift systems tend to be used in order to achieve better space utilisation through stacking.
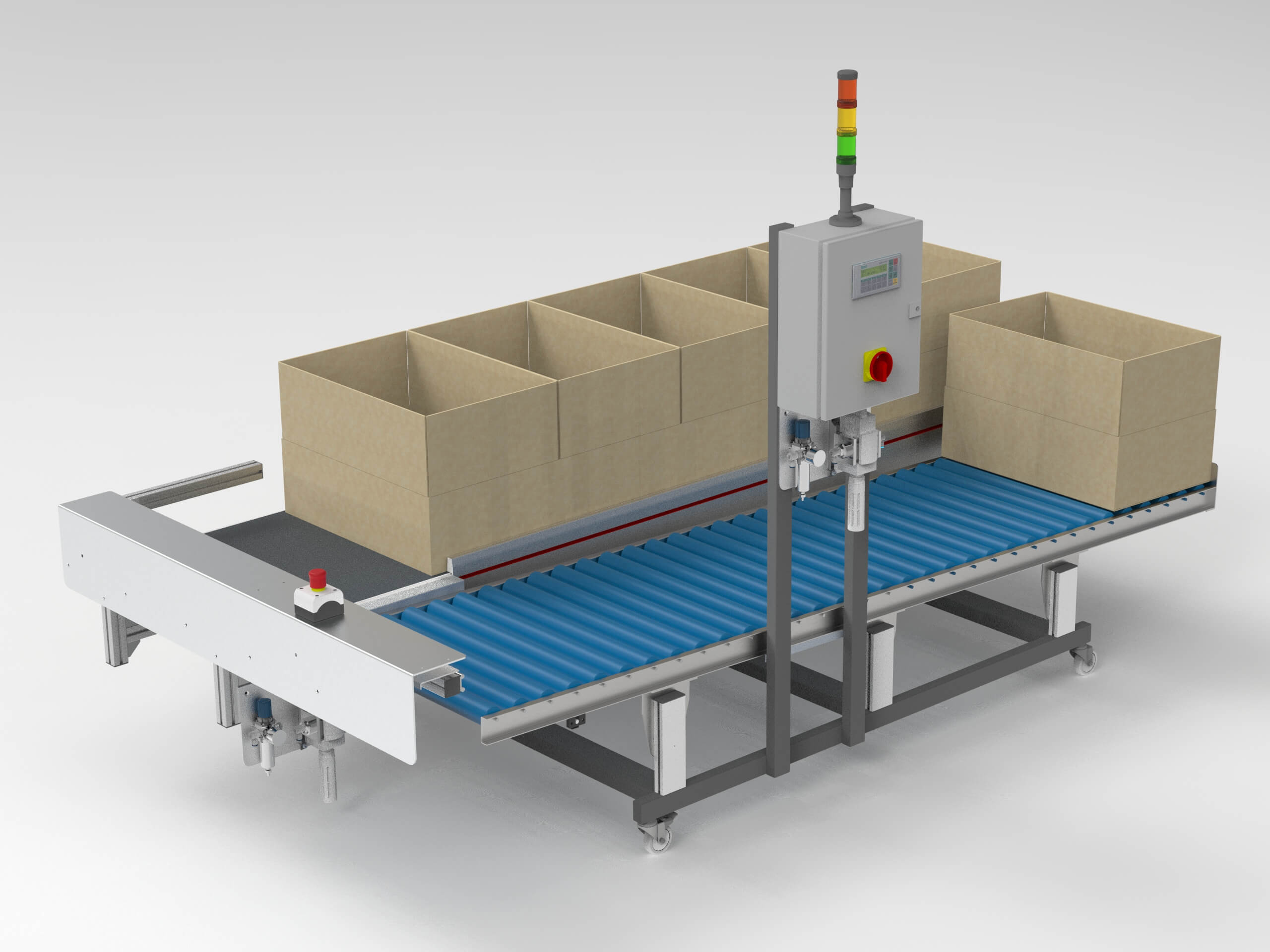
Conveyors with Pneumatic Shifting Units
Förderbänder mit Querschiebevorrichtung kommen zum Einsatz, wenn die Aufgabe leerer Behälter und die Abnahme gefüllter Behälter an einer Stelle erfolgen soll.
Bei dieser Pufferanlage werden die Behälter in einem U-förmigen Ablauf transportiert, d.h. der Bediener setzt leere Behälter auf einem Förderband auf. Diese werden vorgefahren und am Bandende an einem Anschlag auf dem Gurt aufgestaut. In der Anschlagsposition erfolgt dann üblicherweise die Befüllung des Behälters. Ist der Behälter gefüllt, schiebt ein pneumatischer Arm den Behälter im 90°-Winkel zum Förderband auf eine parallel zum Förderband verlaufende Rollenbahn, die gegen die Förderrichtung des Zuführbandes geneigt ist. Dadurch laufen die gefüllten Behälter nach dem Querschiebeprozess auf der Rollenbahn zurück in Richtung Aufgabeposition.
Dieser Ablauf empfiehlt sich insbesondere, wenn die Befüllung z.B. durch ein Robotersystem o.ä. erfolgt, welches in einem Schutzzaun angebracht ist. Dabei befindet sich der Bediener außerhalb des Schutzzauns und kann immer leere Behälter nachschieben und auf der Rollenbahn im gleichen Zyklus gefüllte Behälter entnehmen, ohne in den Zyklus der Produktionsmaschine eingreifen zu müssen.
Nachteilig an der Kombination aus Förderband und Rollenbahn ist dabei die schlechtere Flächennutzung, die maximal 50% beträgt, da das Förderband mit leeren Behältern gefüllt wird und der gleiche Platz als Leerplatz für die später gefüllten Behälter auf der Rollenbahn vorgesehen werden muss. Um diesen Nachteil zu beheben, kann statt der Rollenbahn ein zweites Förderband mit einem weiteren Querschieber eingesetzt werden. Hier ist es lediglich erforderlich, dass ein Behälterplatz leer gelassen wird, um den ersten Querschiebevorgang zu ermöglichen. Wenn die Förderbänder z.B. Platz für jeweils zwei Behälter bieten, so muss ein Platz freigelassen werden, d.h. 75% Nutzungsgrad. Bei Platz für jeweils 10 Behälter auf einem Förderband, muss ebenfalls nur ein Platz freigelassen werden, d.h. 19 von 20 Plätzen und somit 95% der Förderbandfläche können genutzt werden. Dabei können die Behälter einen kompletten Umlauf fahren, d.h. sie kommen im befüllten Zustand dort wieder an, wo sie als Leerbehälter aufgegeben worden sind.
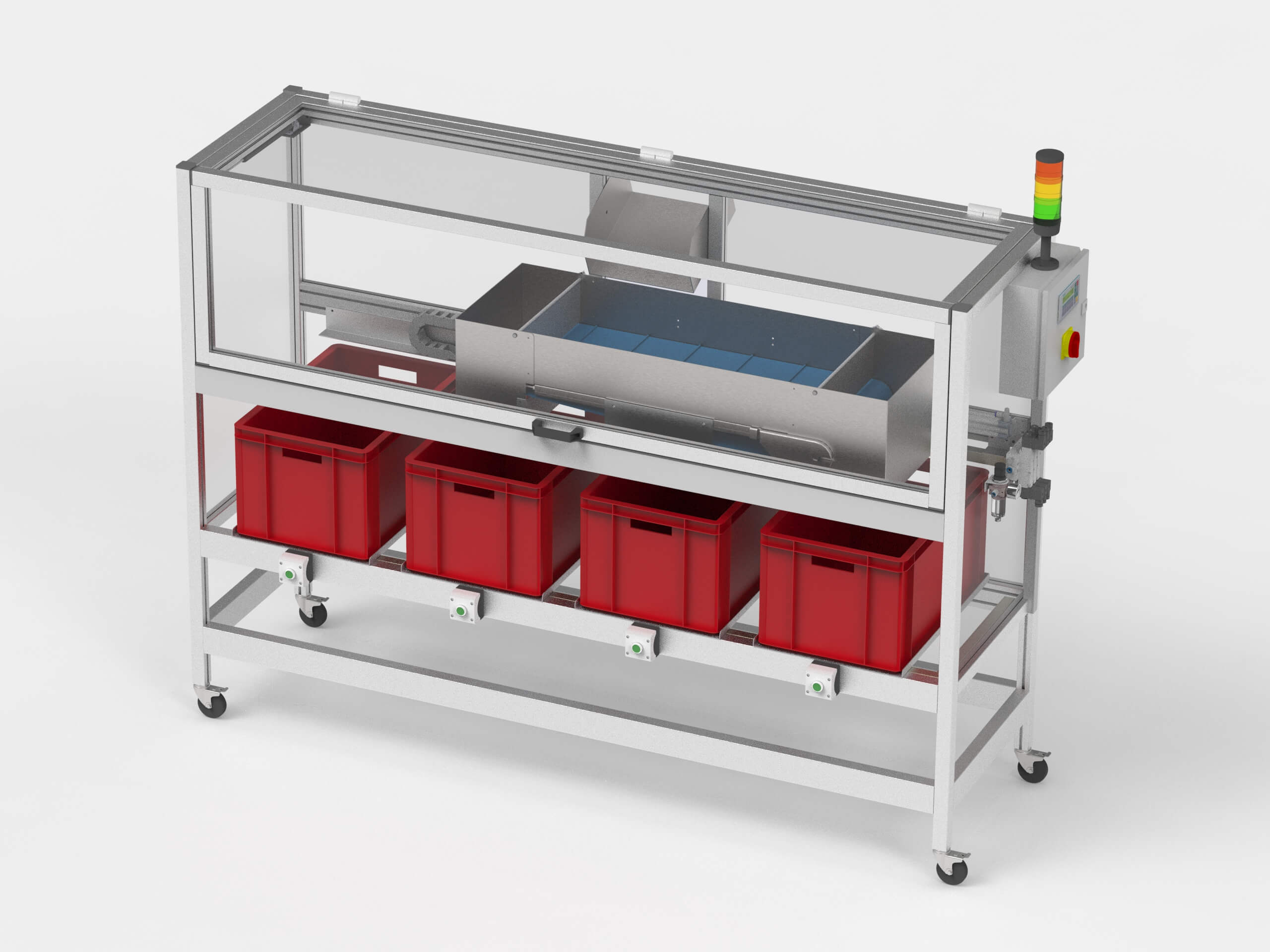
Linear Buffer Conveyors
If very little space is available and only a relatively small number of containers need to be filled, a linear conveyor belt is often a very efficient solution. Here, the containers are arranged below a conveyor belt, which can be moved pneumatically or electrically in the longitudinal direction and has a reversible drive.
The material is then fed from above in the centre of the buffer.
The length of the conveyor belt is adjusted depending on the container dimensions and the installation situation. Depending on the conveying direction, either container 1 or container 3 can be filled, for example. If the conveyor belt is moved linearly by one position, container 2 or 4 can be filled accordingly.
If required, further stop positions can also be provided, e.g. to avoid cones of material. It is also possible to install distributor rockers or distributor diverters at the outlets of the conveyor belt in order to realise even more discharge positions.
This solution is extremely space-saving, as virtually only the base area of the containers is required. The distribution technology is arranged above the containers and does not require any significant additional space. The containers are generally accessible at all times and can therefore be removed or set up empty independently of the machine cycle.
As only the conveyed goods are transported here, virtually all container types can be used (KLT, cartons, bags, mesh boxes, etc.). As the containers are not transported, dimensional stability etc. is not important here. A container mix is also possible without any problems, provided that appropriate positioning can be realised at the discharge positions of the movable conveyor belt.
Depending on the required size, these systems are designed to be mobile so that they can be used variably at different locations.
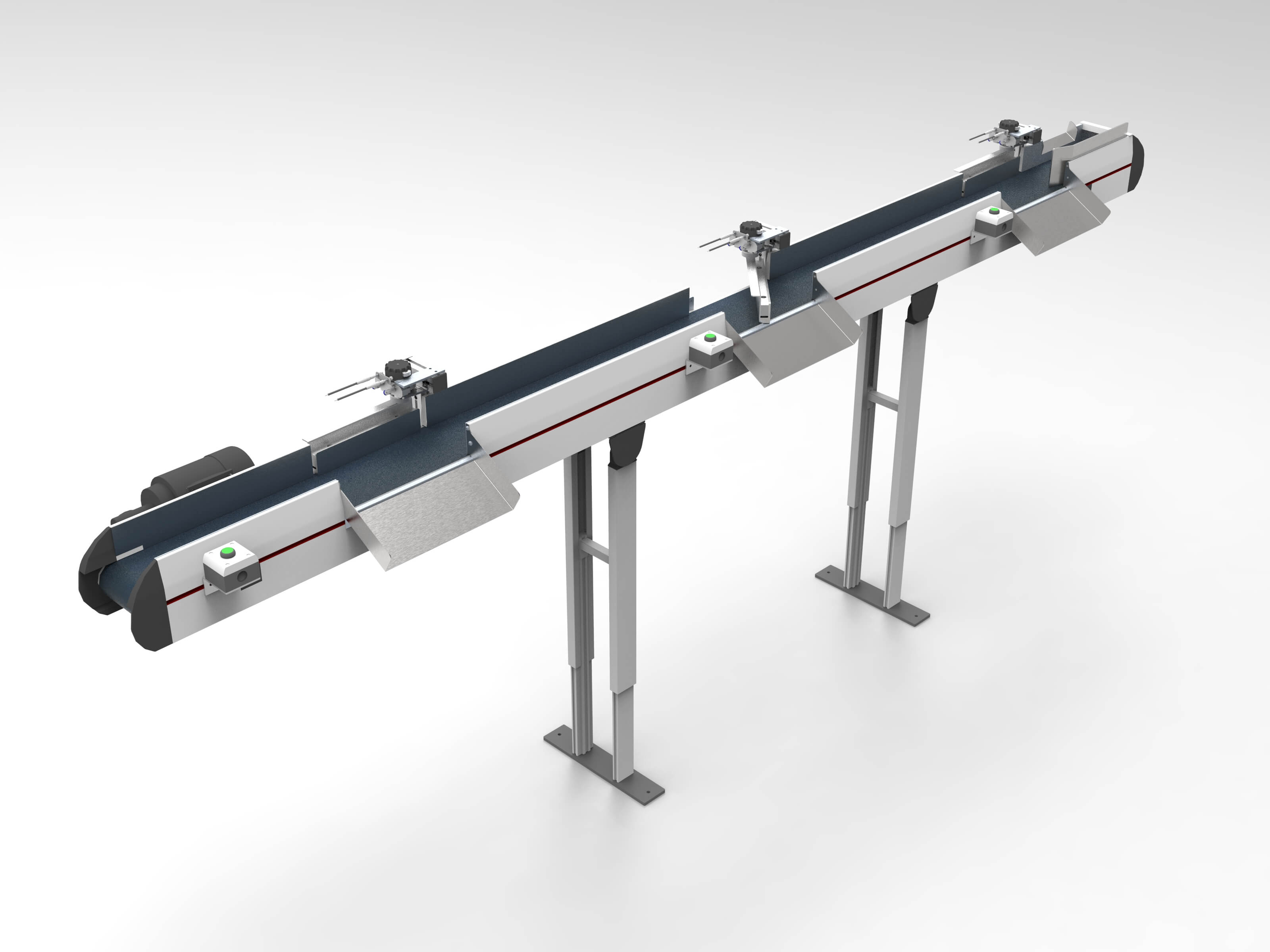
Conveyors with Discharging Units
As with the concept of the linear conveyor belt, containers can also be filled using a conveyor belt with multiple outfeeds. In this case, a conveyor belt is mounted above the containers to be filled. The side guide of the conveyor belt is then removed at each container position and a diverter is installed there instead, which diverts the flow from the conveyor belt to the side. Once all the diverters are closed, they serve as side guides and the goods are mounted to the end of the conveyor belt.
In this way, virtually any number of discharge points can be defined, which can be either very close together or far apart. The solution can therefore be used for space-saving applications in which the containers to be filled can be placed directly next to each other. However, this concept can also be used to supply larger containers or different storage bunkers to automatic assembly machines, for example.
As with the linear conveyor belts, only the goods are transported here, not the containers. The system can therefore be used flexibly for different container types.

Multi-Level Conveyors with Lift
Multi-level conveyor belts in combination with lifts are used, if the required buffer capacity or the autonomy of the container storage system needs to be large or only limited space is availabl. Here, the containers are stored and retrieved on several conveyor sections one above the other and made available at the filling position.
Depending on the requirements, systems with a lifting station are used in combination with the floor conveyor belts or, in special cases, systems with two lifting stations. In systems with a lifting station, one level must remain free in the level buffer. The other levels are filled accordingly with empty containers. However, the first filled container is then transported to the still empty storage level before the next empty container can be provided.
When using two lifting stations, on the other hand, all levels can be fully utilised, i.e. space utilisation is maximised. In this case, filled containers can be stored on one level and empty containers can be supplied for filling from the same level at the same time. As a rule, this also reduces the time required to provide a new, empty container.
A strict FIFO can also be maintained in a system with two lifts, which is generally not possible with just one lift. This can be important, for example, if the buffer system is integrated into a process in order to allow components to cool down or harden before they are further processed.
In practice, most multi-level conveyor belt systems are designed to accommodate containers. Depending on the component size and geometry, however, individual parts can also be buffered.
Due to the usual size of such systems, multi-level conveyor belt systems with lift systems are usually permanently installed and must also be equipped with appropriate protective enclosures or considered very carefully in terms of safety.
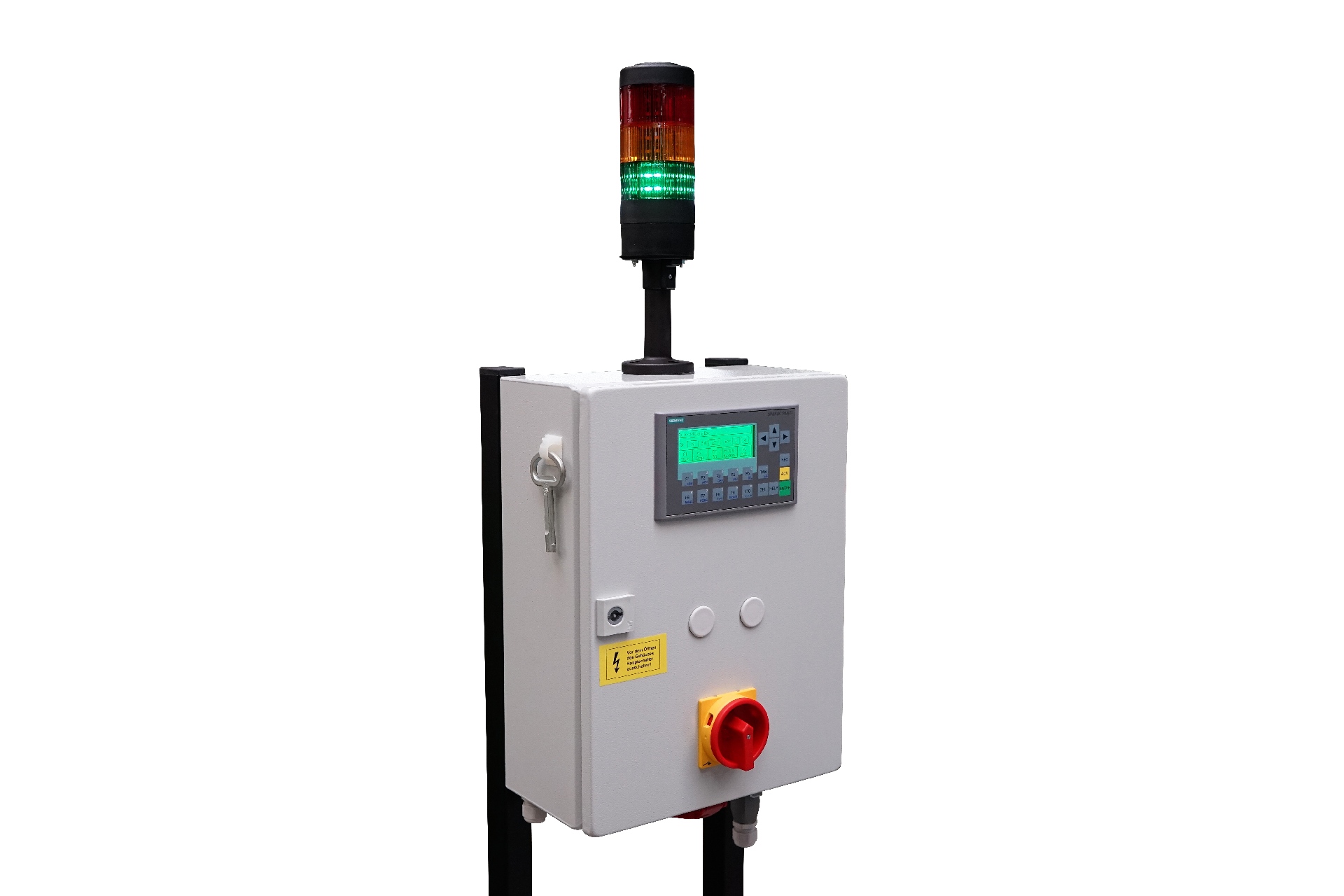
Common Control Functions for Buffering Systems
Most buffer systems require the use of a control system, especially if, for example, a certain quantity of components is to be stored and transported in a container.
Depending on the complexity of the systems and the desired functionalities, the buffer systems can be controlled via existing control systems on production machines, etc. This would be the simplest and cheapest case. This would be the simplest and most favourable case.
In most cases, however, the buffer system is controlled separately, which is then connected to the production system and possibly other transport systems, etc. via an interface. As a rule, the following basic functions are covered:
-
Counting Function, i.e. a container change should take place after a certain number of components or machine cycles. For this purpose, a corresponding target quantity per container is entered in the control system. The counting function usually also includes an input option for a cavity number, i.e. a multiplier for how many parts are produced per machine cycle or per signal.
-
Time Function - as alternative to counting can be useful in certain cases, i.e. the container change takes place after a certain time. This function is required, for example, if there is no signalling evaluation of the production quantity or no connection to the production machine.
-
Follow-Up Time, as there is always is a certain distance between the place where the product is created (e.g. in the mould of a machine) and the container to be filled. This means that the counting pulse takes place before the product arrives in the desired container. If, for example, the component lands on a conveyor belt after the production process and is only then transported into the container, the time required for the transfer must be determined. Once the target quantity has been reached, the conveyor belt must therefore first run continuously for this time until the counted part has been transported into the container.
Other possible control functions include counting the components using a weighing system, which is connected to the control system depending on the product and the required accuracy. Reference weights are stored for each item and a desired target number of items or a target weight per container is requested.
There are also functionalities in which different components are entered with their corresponding parameters (keyword: recipe management). This simplifies operation when different, recurring items are to be produced and buffered.
Depending on customer requirements, various displays, connectors, interfaces, cable lengths, control cabinet designs, signal lights, acoustic elements, operating elements, etc. can be integrated.
Do you have any further questions about our buffer systems? We are available for you at any time via telephone on +49 2261 9431-0 or e-mail or simply use our contact form.