Statically Charged Goods
Typical Problems:
- Plastics usually have a high electrical insulation resistance and can therefore become electrostatically charged before or during the conveying process.
- The components attract dust and dirt and thus influence the product quality.
- Electronic components that are transported on a conveyor belt can be damaged by static charging of the belt.
- Highest cleanliness is required for applications in medical technology
- High electrostatic charges on components can lead to spontaneous discharges and damage components on a conveyor belt (e.g. bearings in rollers)
- High electrostatic charges on conveyed goods or machine parts can lead to life-threatening electric shocks
- Fire and explosion hazard in case of accidental discharge
- Conveyed material sticks to the belt and "go round and round"
- Materials stick together and are difficult to process further
Solutions for the Conveyor Technology:
All MTF devices are designed in such a way that they cannot become electrostatically charged through their own operation. Nevertheless, electrostatic charges can be transferred to the units by the material being conveyed or separated. To avoid the problems associated with this, MTF Technik offers various solutions:
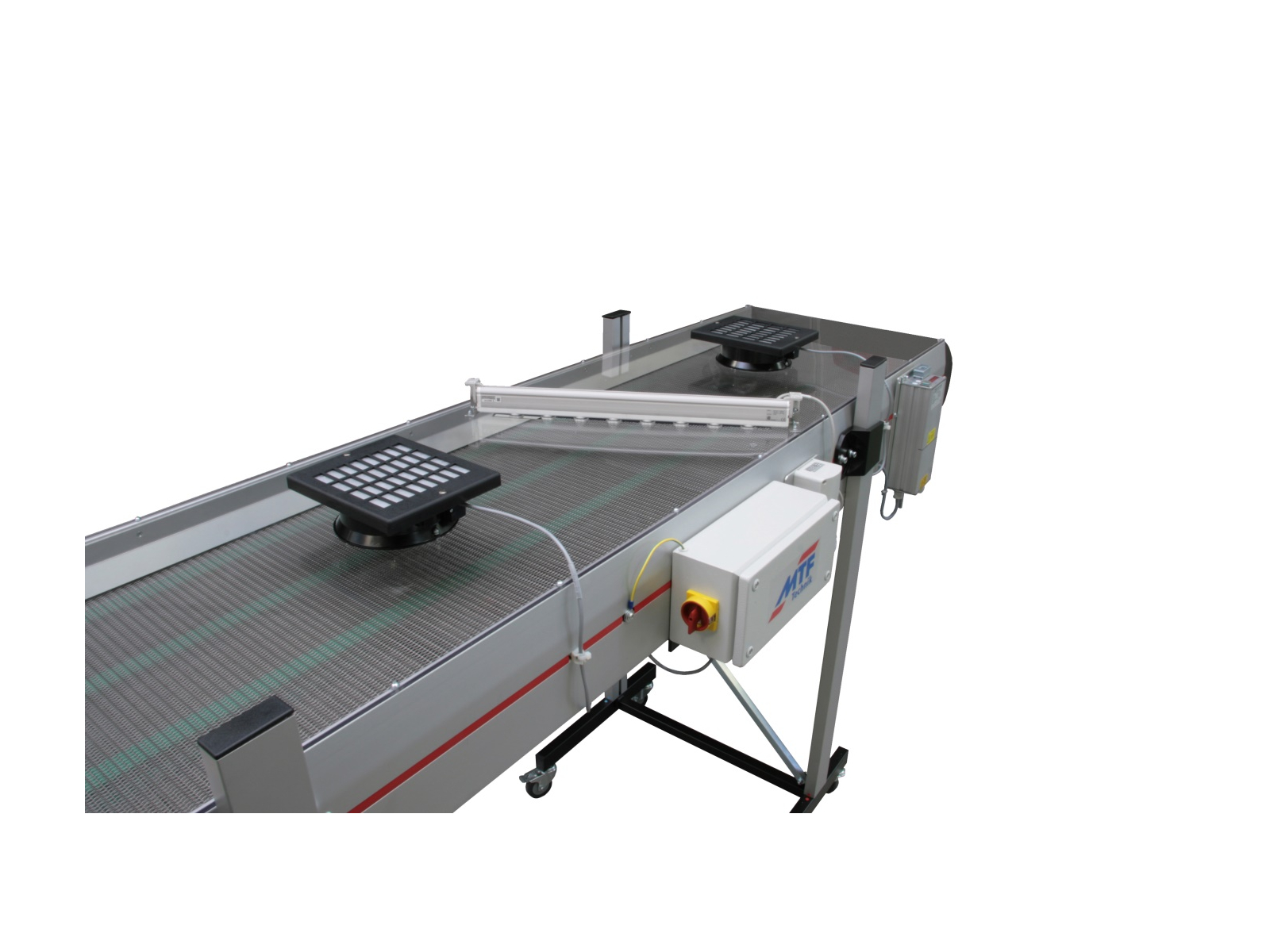
Ionisation Devices
Non-conductive materials (insulators) cannot be discharged by earthing. To neutralise the charges, e.g. on plastic components, air ionisation units on conveyor belts and separators are suitable. The ionisation units generate a large number of positively and negatively charged ions that serve as mobile charge carriers in the air. These ions are attracted to the electrically charged surfaces and particles, which then leads to neutralisation.
Ionisation units are available in different versions from different manufacturers. Which solution is used depends on various factors, e.g.:
- Desired manufacturer of the ionising units according to customer specifications.
- ype and quantity of parts to be discharged
- Material speed
- Ambient conditions
- Area of application (on a conveyor belt, on a separator)
- Working width
- Working distance
etc.
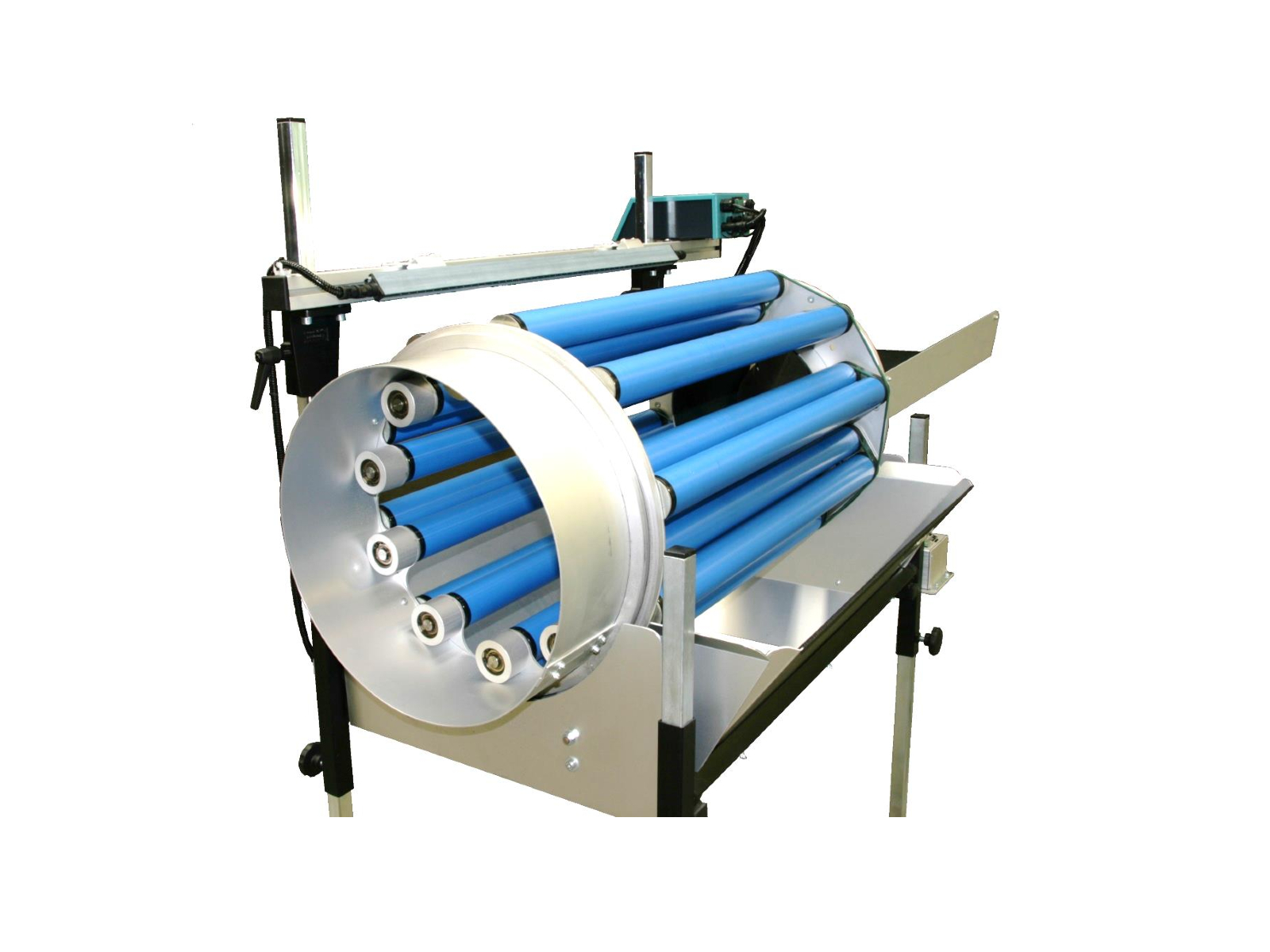
MTF Technik usually attaches the ionisation units to the conveyor belt on belt covers or in the area where the parts are discharged. Depending on the degree of electrostatic charging of the parts, it may also be necessary to attach several ionising units to the conveyor belt. This may be the case, for example, if plastic parts are fed onto the conveyor belt very hot. If the parts are then discharged directly at the feed point (e.g. also via an ionisation unit above the mould in an injection moulding machine), the parts are largely neutralised when they hit the conveyor belt. However, as a result of cooling during the conveying process, internal friction in the parts can create new charges which then have to be removed at the end of the conveyor belt.
Discharge bars can also be mounted in transfer bonnets or freely above a conveyor belt or also above a separating drum. Discharge bars can also be equipped with compressed air nozzles, which can then be controlled, for example, via corresponding pneumatic valves.

There are many different types of belts made of different materials, such as PU, PVC, felt, polyester fabric, silicone, rubber, etc. The conveyor belts are usually made of different layers and often also have a fabric that serves as a backing layer. In most cases, the conveyor belts are made up of different layers and often also have a fabric that serves as a backing layer.
Most of the above-mentioned belt materials are insulators (e.g. PU, PVC), i.e. they do not dissipate any static charges. Nevertheless, many belts are described as "antistatic" by the manufacturers. This refers in each case to the running side of the belt, i.e. the inside, which is in contact with the conveyor belt. In this context, "antistatic" means that the running side of the belt is equipped with e.g. electrically conductive threads (usually carbon threads) and thus prevents the belt from charging itself by sliding over the belt body. Any charges generated by the slipping process are discharged directly via the aluminium frame of the conveyor belt.

However, this says nothing about whether, for example, the surface of the belt, the so-called carrying side, also becomes charged over time due to the constant exposure to electrostatically charged conveyed material. This can lead to parts then "sticking" to the belt.
For special applications, such as the transport of highly sensitive circuit boards in the electrical industry or conveyor belt applications in potentially explosive atmospheres (ATEX), even higher demands must therefore be met in some cases. For this purpose, MTF Technik offers e.g. the Belt No. 44 This is a belt which, according to the manufacturer's data sheet, has a surface resistance of less than 3 ∙ 108 Ω and a contact resistance of less than 1 ∙ 109 Ω. According to EN 13463-1, it can be assumed that electrostatic charging is avoided if the surface resistance is less than or equal to 1 ∙ 109 Ω.
We can already illustrate the difference with an installation tester, for example. Even though electrostatic charges can easily amount to several tens of thousands of volts, a test with an installation tester and a voltage of max. 500V already shows clear differences. For example, we measured the surface of MTF Belt No. 44 and MTF Belt No. 45. In the case of Belt No. 44, a test voltage of 116 volts already produces a measurement result of 0.04 MΩ. In the case of Belt No. 45 (PU surface), no resistance can be measured despite a maximum test voltage of 535 V, i.e. this is an insulator. Even though the test setup in this form does not correspond to any standard, it nevertheless shows very clearly the difference in the conductive behaviour of different belt materials.
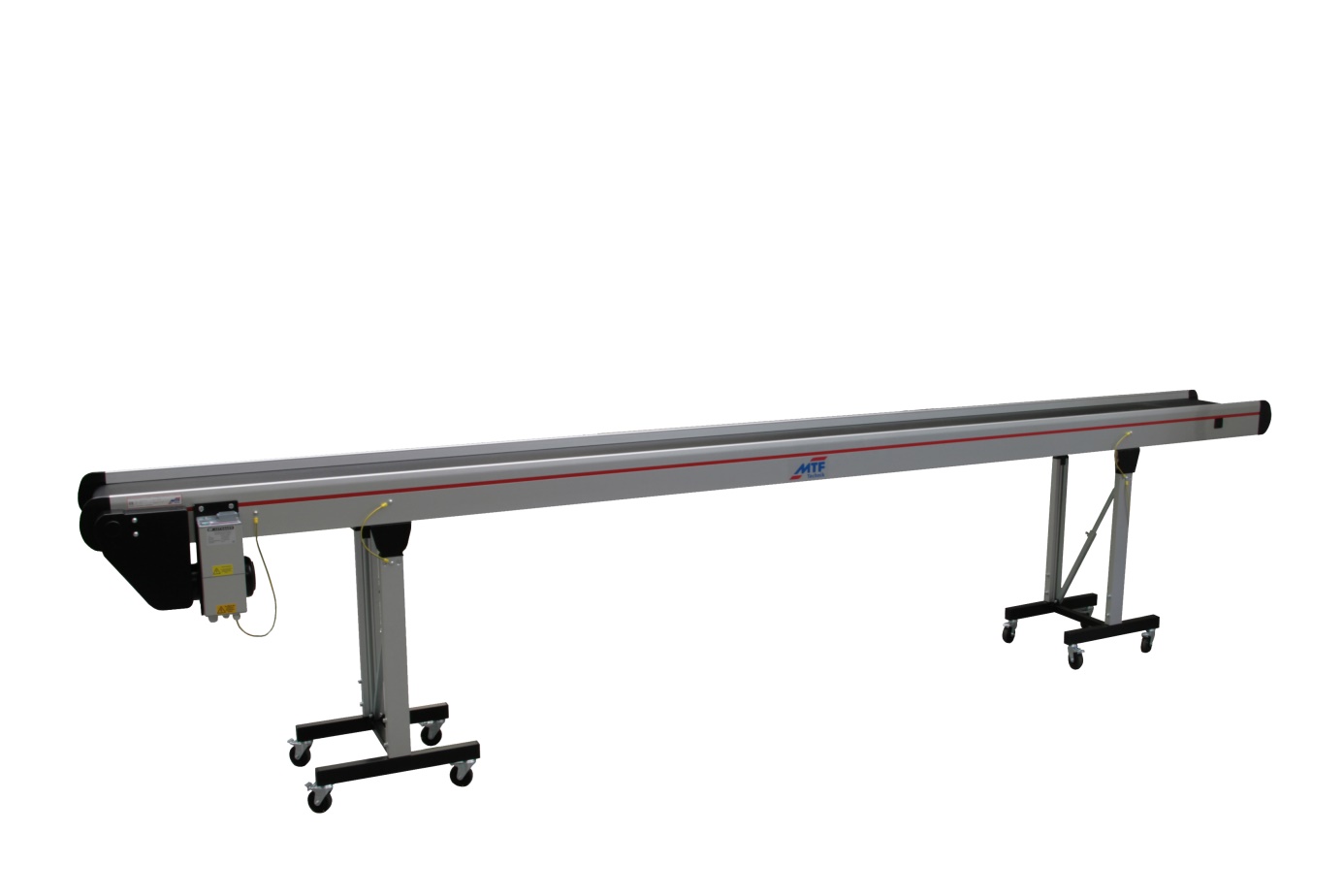
Additional Earthing
Each device from MTF Technik is equipped with a standard-compliant earthing system. In most cases, this is realised by electrical connection cables and/or via additional earthing lugs. In case of special applications, e.g. transport of highly electrostatically charged plastic parts, additional earthing can help to dissipate the charges.
In order to remove unwanted charges from the carrying side of a belt, electrically conductive brushes can be used, for example, which are mounted at the belt infeed. These pick up any charges that may be sitting on the belt and carry them away so that a "neutral" belt is ready in the area of the parts feed. With each revolution of the belt, it is thus grounded again. Fibres made of carbon or stainless steel, for example, are used here.
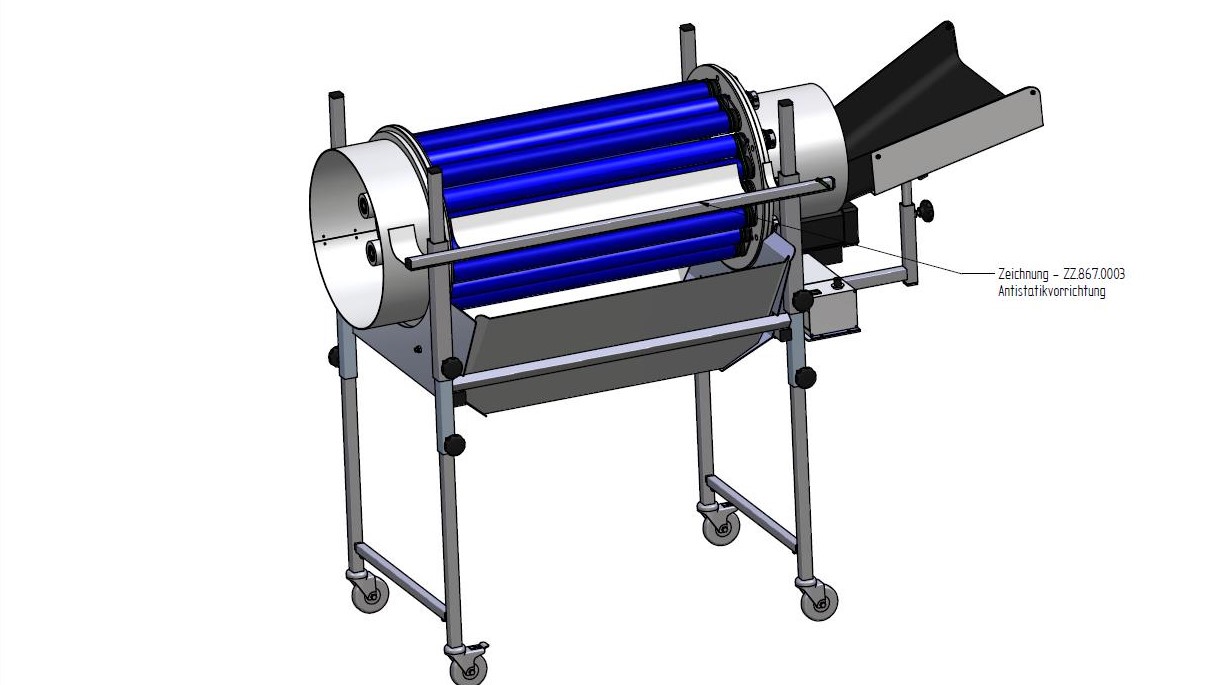
Statically charged separation material can also cause problems in separation drums. Here, there is a risk that the charges are transferred to the PVC rollers of a roller separation drum, for example.
In addition to the use of an ionisation bar above the separation drum cage (see above), a thin earthed stainless steel foil can also be placed on the rotating drum cage, for example. This is optionally offered by MTF Technik as a clip-on device for the underframe and can also be retrofitted to existing systems. The stainless steel foil then sweeps over the drum cage and discharges the charges.
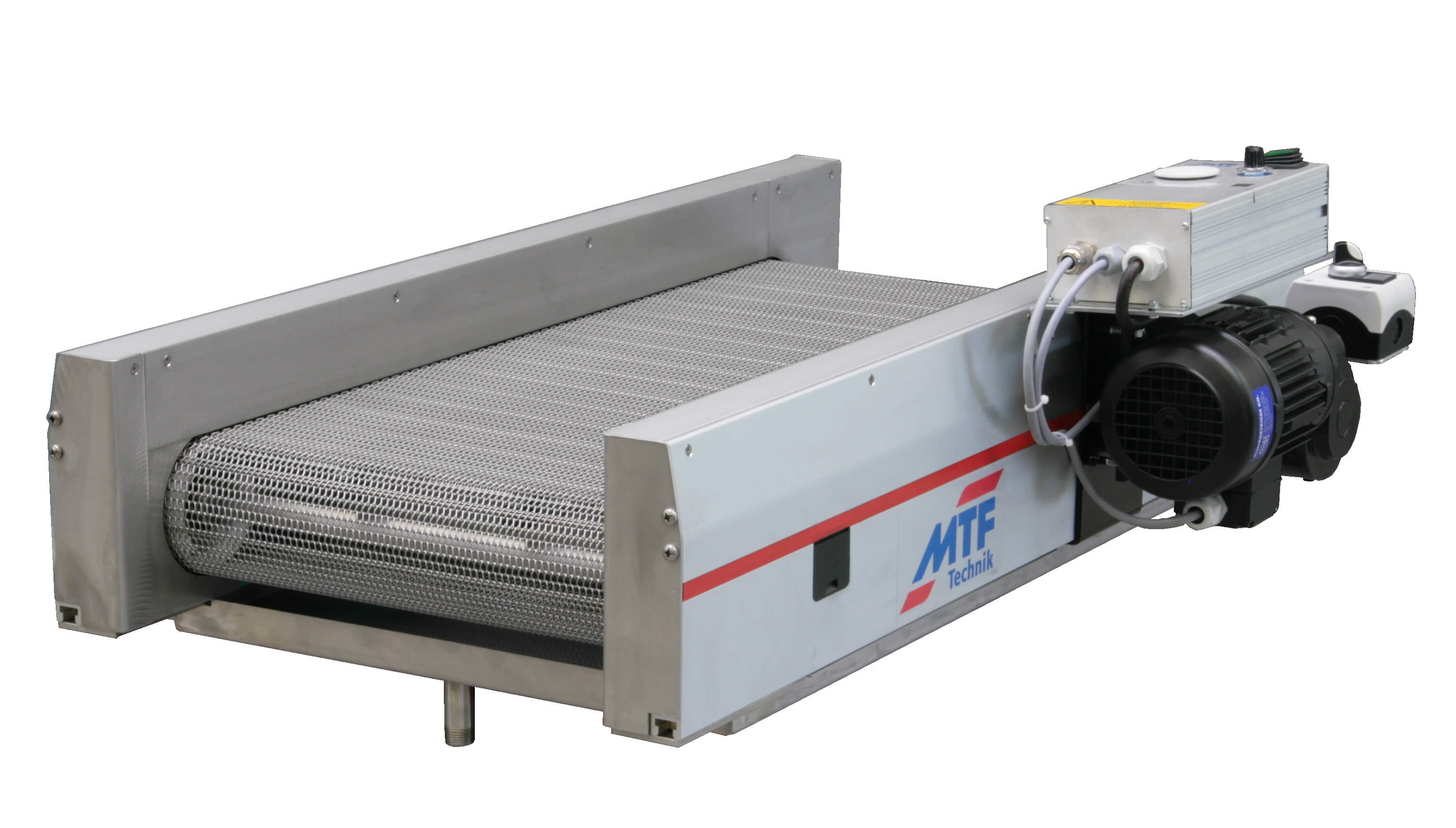
Steel Hinged Plate Conveyors and Wire Mesh conveyors
The steel hinged plate belts as well as the steel mesh conveyor beltsfrom MTF Technik are perfectly suited to dissipate static charges on components due to their electrically conductive properties. The hinged plates are earthed accordingly via the contact to the belt body and the earthing of the drive.
However, the costs here are significantly higher than for a belt conveyor, so that belt conveyors with special accessories are more commonly used in practice.
Do you have any further questions? We are available for you by telephone at +49226194310 or info@mtf-technik.de or use our Contact form.