This demonstration video shows how an area metal detector works on a conveyor belt.
Metal Detection at the Conveyor
Typical Problems with the Material:
- Protection of a plastic granulator or the granulator knives from damage by foreign substances (metals)
- Detection of metallic contaminants in products for quality control, e.g. in the food industry or in plastic packaging
- Quality control of metallic inserts (presence check of metallic parts)
- Detection of impurities in shredded material
Solutions for the Conveyor Technology:
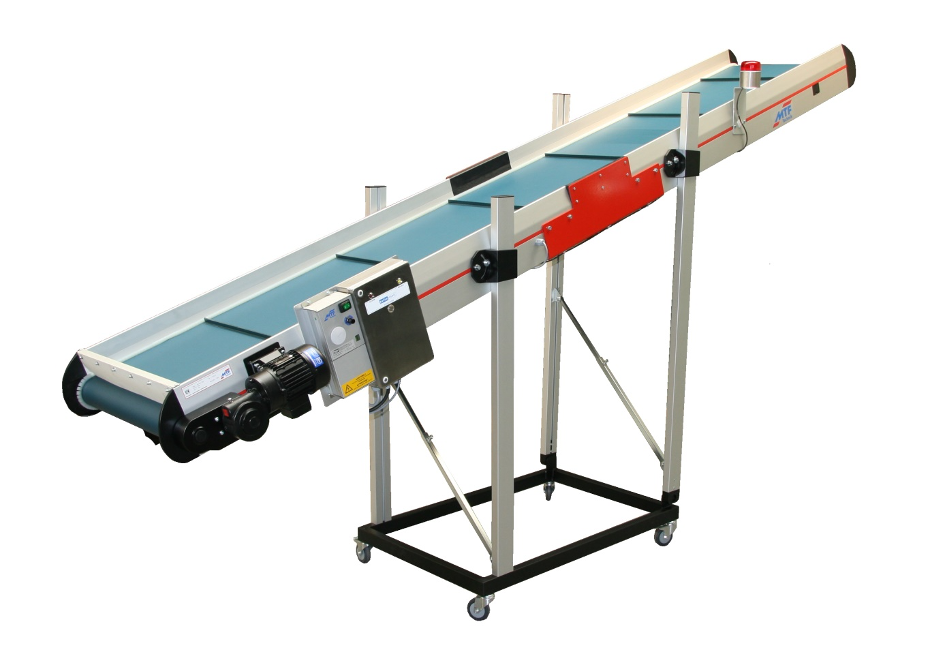
Area Metal Detectors
Area metal detectors are used to detect metallic contaminants in the conveyor flow of piece goods and unit loads with material heights up to a maximum of approx. 100mm. Magnetic and non-magnetic contaminants can be detected (steel, stainless steel, aluminium, copper, etc.). They can be integrated into the frame of the conveyor belt or mounted underneath chutes, for example.
If metal is detected, various measures can be taken via the control unit and connected evaluation systems, e.g.
- Belt stop, restart via manual reset
- Belt reversal for an adjustable time
- Signal horn
- Signal light
- Control of an ejection device, e.g. pneumatic
- Event counter
- etc.
The sensitivity depends largely on the distance of the metallic contamination from the detector surface (see sensitivity diagram at the bottom of this page). Depending on the manufacturer of the detectors and the general conditions, the sensitivity is subject to certain fluctuations.
Demonstration video of an area metal detector see below

Tunnel Metal Detectors
Tunnel metal detectors on the conveyor belt are used to detect all metals in the conveyor flow and are used for larger material heights. MTF Technik primarily uses separable tunnel metal detectors. Their benefit is that they can be easily integrated into the construction of the conveyor and, above all, the belts can be used as an endless welded version.
Closed tunnel detectors are particularly suitable if, e.g. flat conveyor belts are to be pushed completely into the tunnel or if the conveyed material passes through the detector via chutes or in free fall. They have an even higher sensitivity than separable versions.
The sensitivity of the detectors depends primarily on the clear passage height. The smaller the passage height, the higher the sensitivity. Steel parts are detected much better than e.g. parts made of stainless steel (rough guide value: factor 2) or other metals such as copper, aluminium, brass (here the factor is approximately between 1.2 and 1.8).
Tunnel metal detectors require a special construction of the conveyor belt with a metal-free zone adapted to the detector, i.e. in this area the conveyor belt body, which is otherwise made of aluminium, is completely separated and replaced by a wooden construction. For the best possible detection result, care must be taken to ensure that as few vibrations as possible are transmitted to the detector. Influences from humidity, electromagnetic interference fields, etc. must also be taken into account.
Since the tunnel detectors are very sensitive and also react to disturbances in the direction of the opening, it must be ensured that, for example, no electromagnetic interference fields are too close to the detector (e.g. controls of other systems, motors and drive). Likewise, vibrations should be avoided as far as possible (e.g. forklift traffic next to the device, drop processes of conveyed goods onto the conveyor belt, etc.).
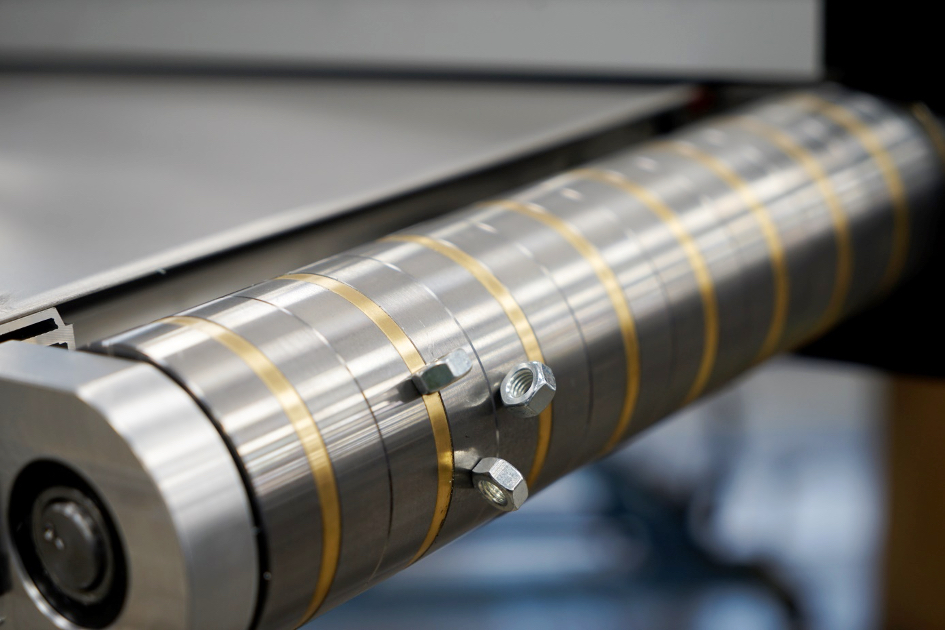
Magnetic Drive Roller
A magnetic drive roller is mounted at the outlet of the conveyor belt (pulling drive). It separates ferromagnetic parts from a continuous conveyor flow and transports them away continuously. Depending on the thickness of the conveyor flow, a combination of magnetic drive roller and plate magnet above the conveyor belt can also be useful.
In this way, the plate magnet pulls the foreign bodies out of the upper product layers, while the magnetic drive roller separates the lower layers of the product stream from foreign bodies.
Demonstration video of the magnetic drive roller see below
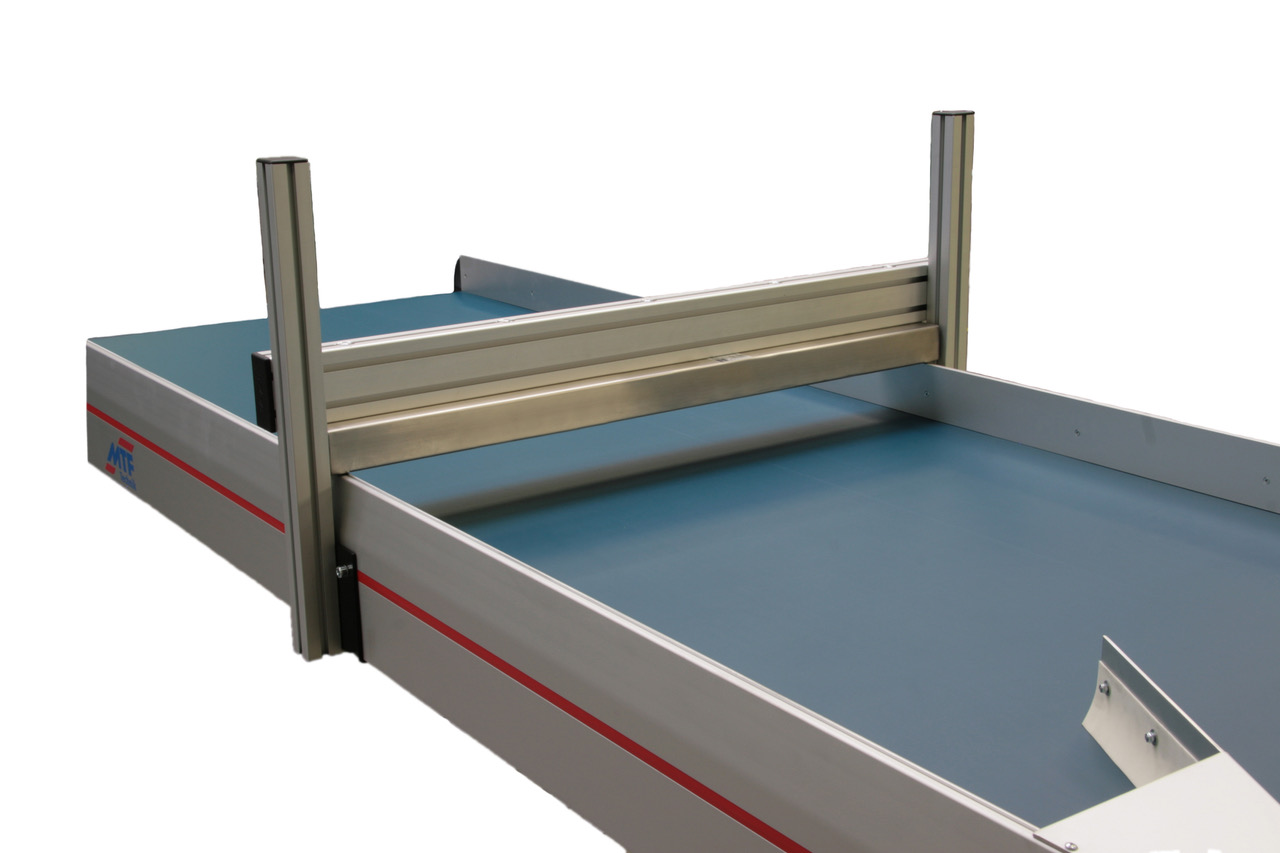
Plate Magnets as Accessory
Plate magnets are used to separate small quantities of larger ferrous foreign bodies from a continuous and easily permeable conveyor flow. They can be arranged e.g. above a conveyor belt, above or below chutes or in free fall. Depending on the task, different magnetic materials can be used (ferrite or neodymium-iron-boron).
The advantage of this solution is its simplicity. Plate magnets do not require a power supply or evaluation electronics. They are accordingly easy to integrate or install.
The disadvantage is that the plate magnet must be manually cleaned of any foreign bodies that may have been attracted.
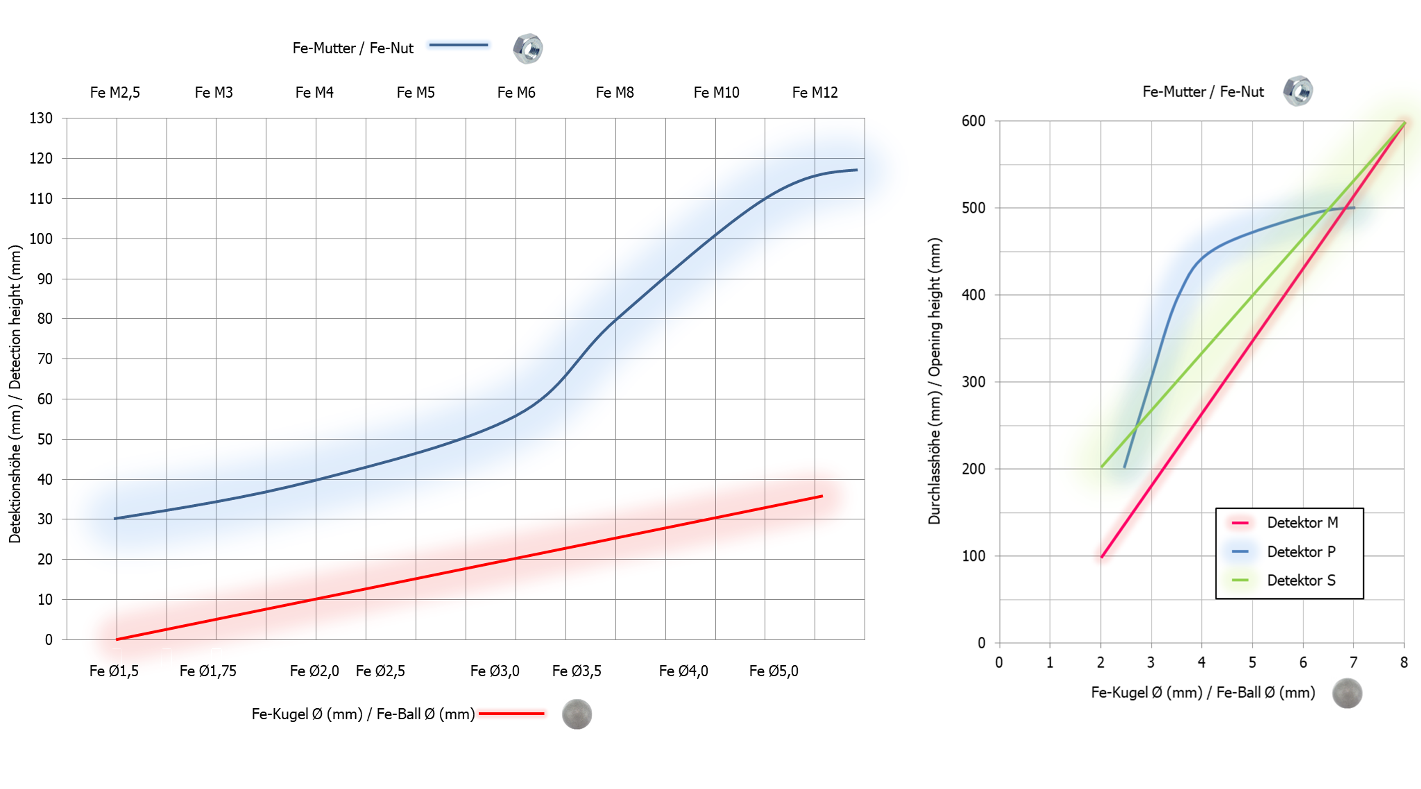
This demonstration video shows how the magnetic drive roller works on the conveyor belt.
Do you have any further questions? We are available for you by telephone at +49226194310 or info@mtf-technik.de or use our Contact form.