Efficient Separation of Components
Typical Problems in Separating Components
-
In injection moulding and die casting production, downstream separation of the usable part and sprue is often required in the production process
-
Sprue removal in the mould, e.g. using sprue pickers, means longer cycle times up to 20%
-
Existing separation devices are often not used with optimum efficiency, i.e. the separation rate is not at 100%
Separating Solutions for Improved Productivity
Separating systems from MTF Technik make a considerable contribution to improving productivity in the manufacture of injection moulded or die-cast parts, as they significantly reduce cycle times compared to separation by means of handling. In addition, the investments made are often amortised within just a few weeks.
However, optimum results can only be achieved if the separation technology is used efficiently. In addition to the parameters of cycle time and number of cavities, the geometry of the moulded part and sprue play a decisive role. A certain difference in the size of the parts is always necessary here - either in height and/or in surface area.
In our guide, you will find an overview of the most important device types with their respective key features:
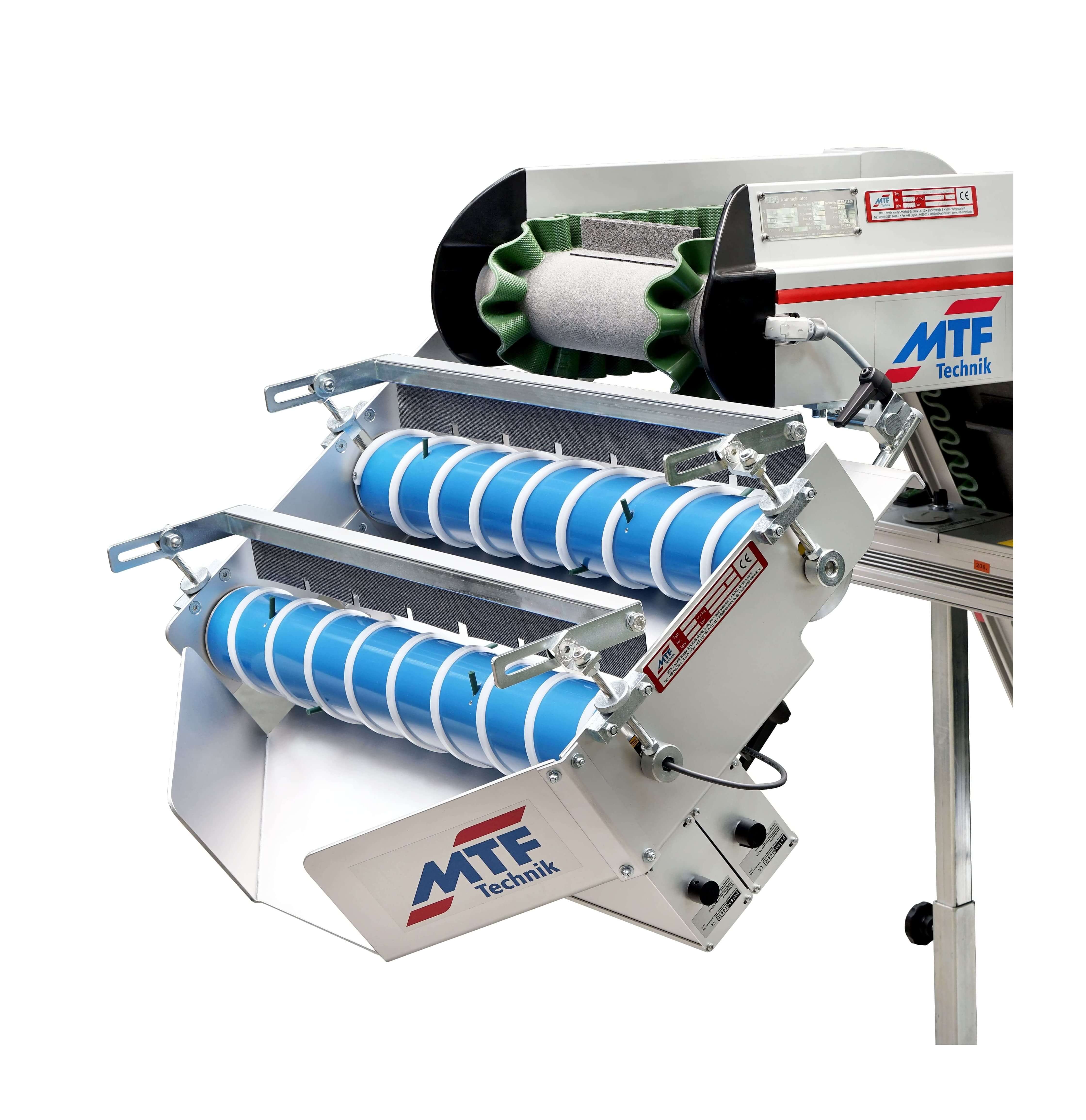
Screw Separators
For most applications in plastic injection moulding, screw separators lead to very good separation results. The space-saving devices can be designed as a free-standing model (e.g. Multi-Separator MSL 600) or as an attachment to the conveyor belt (e.g. Separator SAL 600).
In this case, a rotating roller with an attached screw profile is mounted above a stationary sheet. The separation gap results from the distance between the screw roller and the sheet, whereby the small parts slide underneath the screw and the large parts are pushed to the side.
In order to achieve an optimum separation rate with these devices, a number of design features are important. It is essential that the screw roller is stable and supported on both sides so that the roller is at the same distance from the discharge plate everywhere and does not "wobble". In addition, the rotational speed of the screw must be adjusted precisely to the respective separation task. Some components require a slower separation process, while other parts can be separated better if the screw roller rotates as quickly as possible.
In this context, a separate drive for the screw with integrated overload protection is ideal in order to prevent jamming of parts and ensure optimum work safety - even if it is an attachment on the conveyor belt. This means that the rotational speed of the screw can be controlled independently of the speed of the feed belt. This is particularly important if, for example, the parts are to cool down on the conveyor belt first. In this case, a very slow or intermittent conveyor speed and a fast rotating screw roller are necessary for an optimum separation rate.
Another important detail are flexible spikes, which should be fitted along the circumference of the screw and thus serve to loosen up the material to be separated. As a result, larger parts that may have settled in front of the screw and blocked the passage for the smaller parts are repeatedly set in motion to clear the passage.
A flexible scraper above the screw roller prevents parts from jumping over the screw during feeding - e.g. by a conveyor belt. They bounce against the scraper and are thus fed back into the separation process.
A version for a two-step separation process is available (see photo).
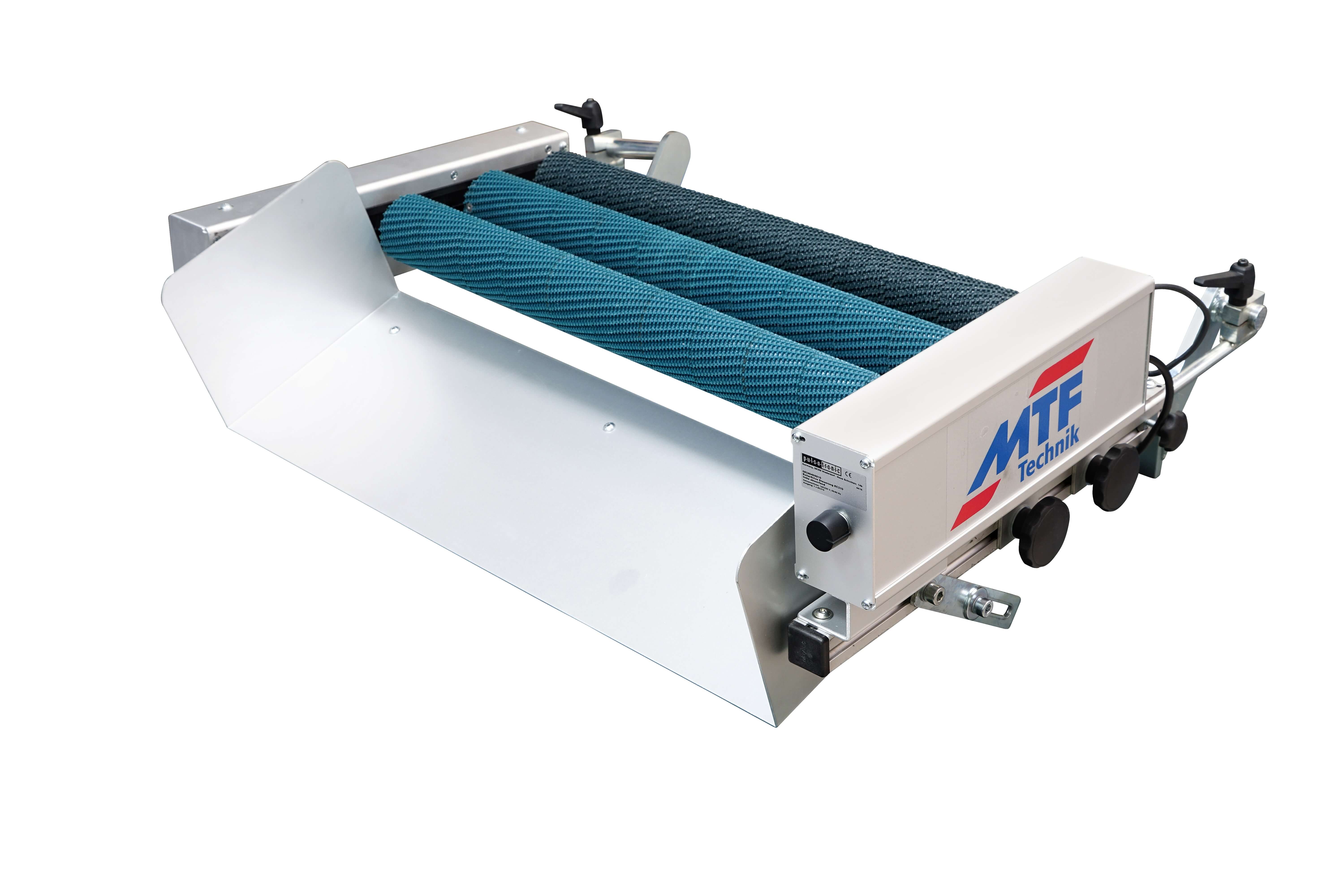
Separating Rollers
A Separating Roller Device, attached to the outlet of the conveyor belt, is suitable in many cases for separating parts and sprues with different surface expansions from one another. In this separation process, the larger, flat sprues run over the rollers, while the smaller parts fall between the rollers. Depending on the type of components, it is also possible to use a Disc Separator. This device is available as an attachment or in a free-standing version.
As with screw separators, the main focus here is on stable, double-sided bearings for the individual rollers and individual speed control in order to achieve optimum separation results.
In addition, different roller coverings should be used wherever possible. Depending on the task and the behaviour of the parts, it may be necessary for the roller coverings to be very entraining or rather smooth.
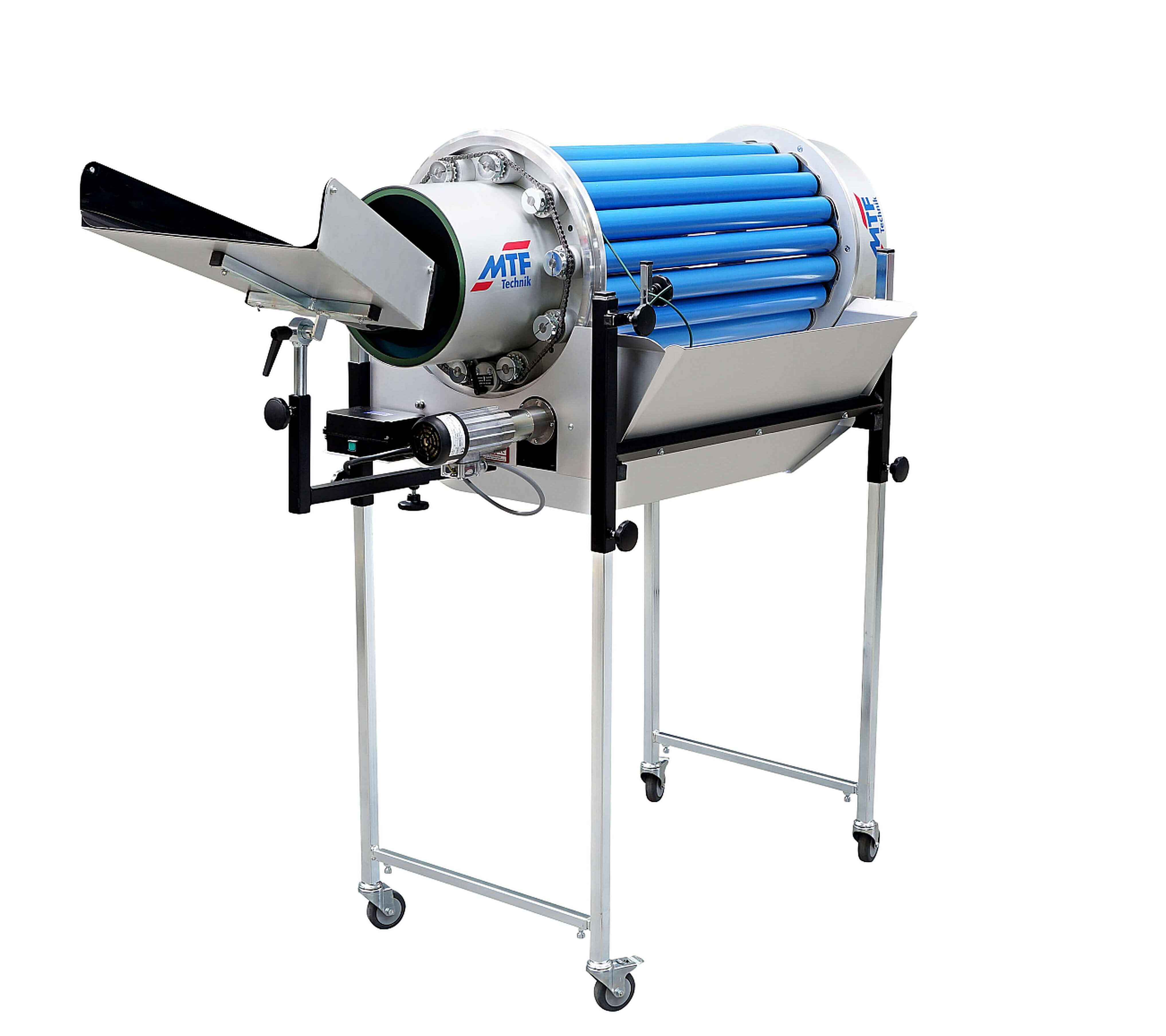
Roller Separation Drums
Separation drums are generally used for larger throughput quantities or component-moulding combinations where circulation can improve the separation result. The circulation process dissolves and separates interlocked parts much better than the separating attachments.
Roller Separation Drums are used to separate components and sprues of different heights. They can be used for a variety of separation tasks. There are separation drums with individual adjustment of the separating gap or devices with central adjustment (see photo).
With individual adjustment, each roller is fixed individually in the drum cage. The distance between two rollers defines the separating gap. As this adjustment is relatively time-consuming, this type of separation drum is only suitable for applications where a machine is occupied with one article for a long period of time or where several similar component/sprue combinations can be separated with one adjustment.
Separation drums with central adjustment of the separating gap, on the other hand, are suitable if a wide range of parts is to be separated. The central adjustment offers quick adjustment - it can be set to a new product combination within a few seconds. Two rollers always form a firmly connected pair, so that only every second gap between the rollers has a separating function. This reduces the number of separating gaps compared to a separating drum with individual adjustment - the maximum throughput is lower.
With roller separation drums, it usually makes sense for the rollers to be driven by a strap tensioned around the cage. This results in counter-rotation of the rollers, which prevents jamming processes. In addition, the rotation of the rollers also increases the separation area within the drum cage. This significantly increases the throughput and the separation rate compared to a drum cage with fixed bars.
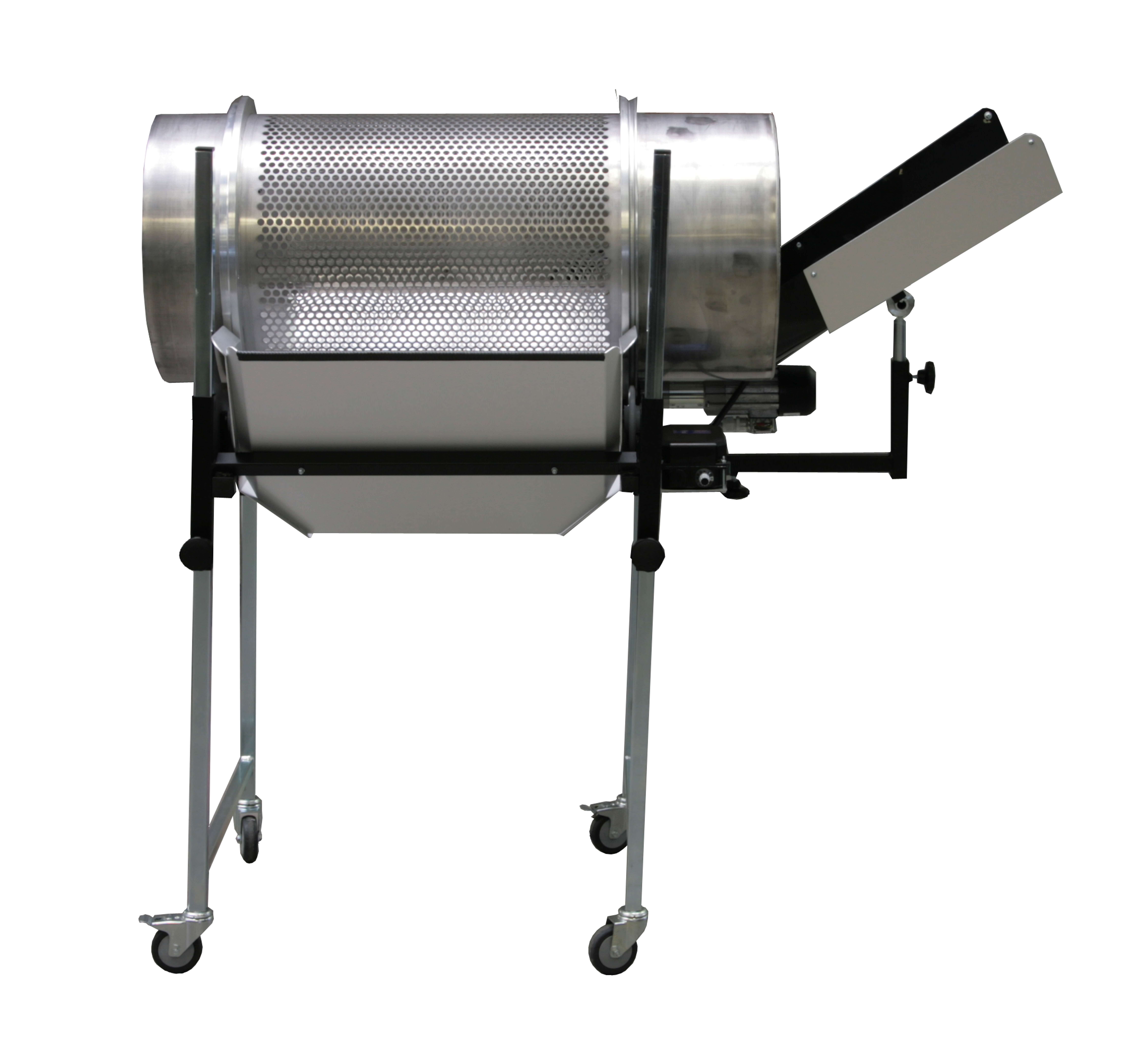
Perforated Separation Drums
Perforated Separation Drums are used when the parts to be separated do not differ in their height but in their surface area (e.g. coins with different diameters but the same material thickness). The advantage of Perforated Drums is their favourable price on the one hand and their high throughput on the other. The entire cage can be provided with holes and if the hole spacing is also very small, the smaller components find many opportunities to fall out of the drum per revolution.
The disadvantage of Perforated Separation Drums is that the hole geometry is fixed and therefore only fits a limited range of parts. However, complete drum cages can be replaced very easily to cover a correspondingly wider range.
Depending on the application, many different materials are used for the barrel cages. In addition to steel and stainless steel cages, rubber or silicone materials can be used here, for example, to ensure the best possible protection of parts and also minimise noise.
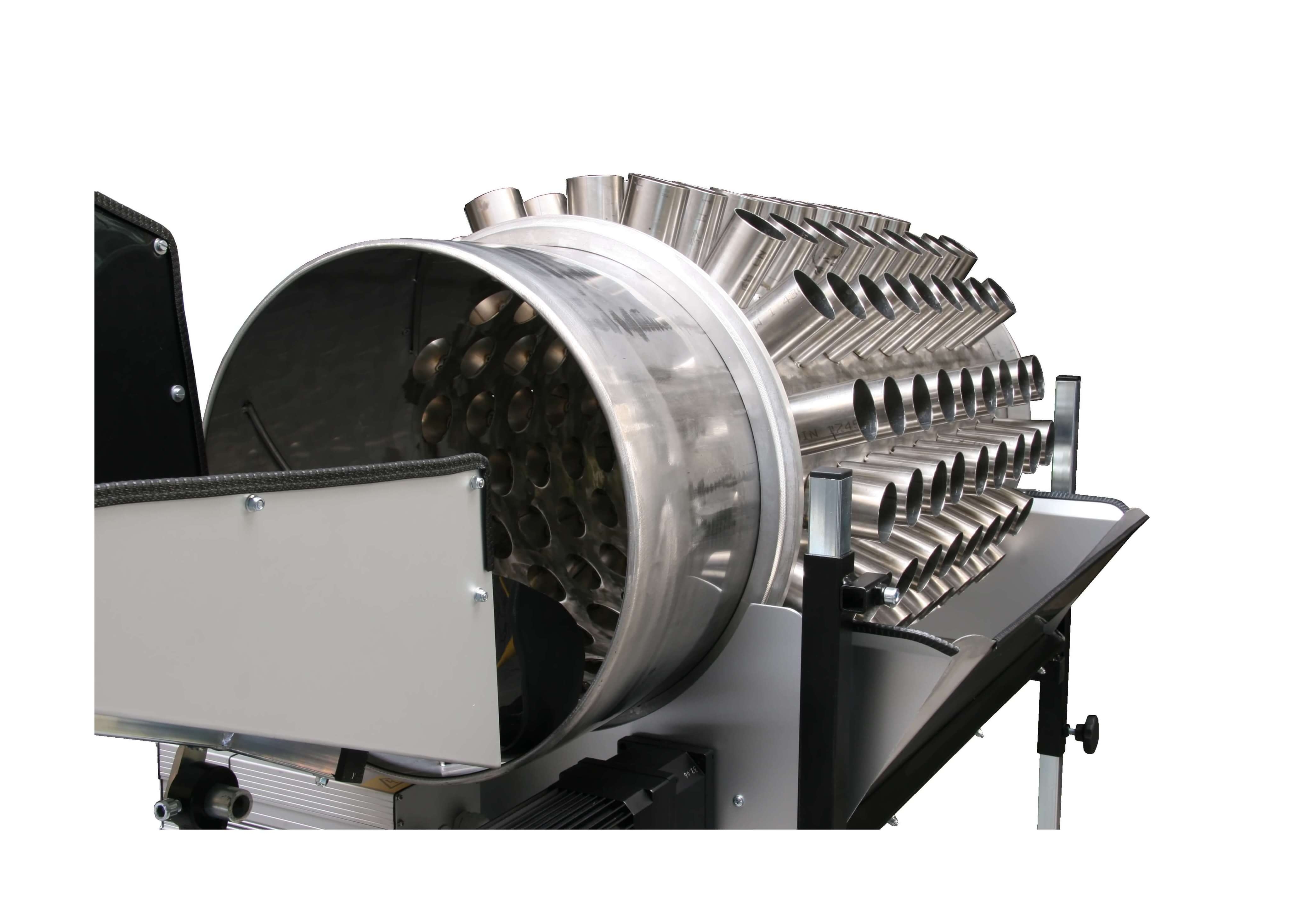
Hedgehog Separation Drums
Hedgehog Separation Drums are a special type of perforated drum for specific part geometries. Developed by MTF Technik, in this process sleeve tubes with same the geometry and size of the holes are attached to the outer circumference of the drum cage as an extension. This ensures that e.g. S-shaped parts, cannot "snake" through the holes. These parts can only dip into the sleeve tube with their tip, but then fall back into the drum cage. The sleeve tubes also prevent, for example, sprues that are prone to snagging from getting stuck in the holes.
The cages are made of stainless steel as standard (see photo).
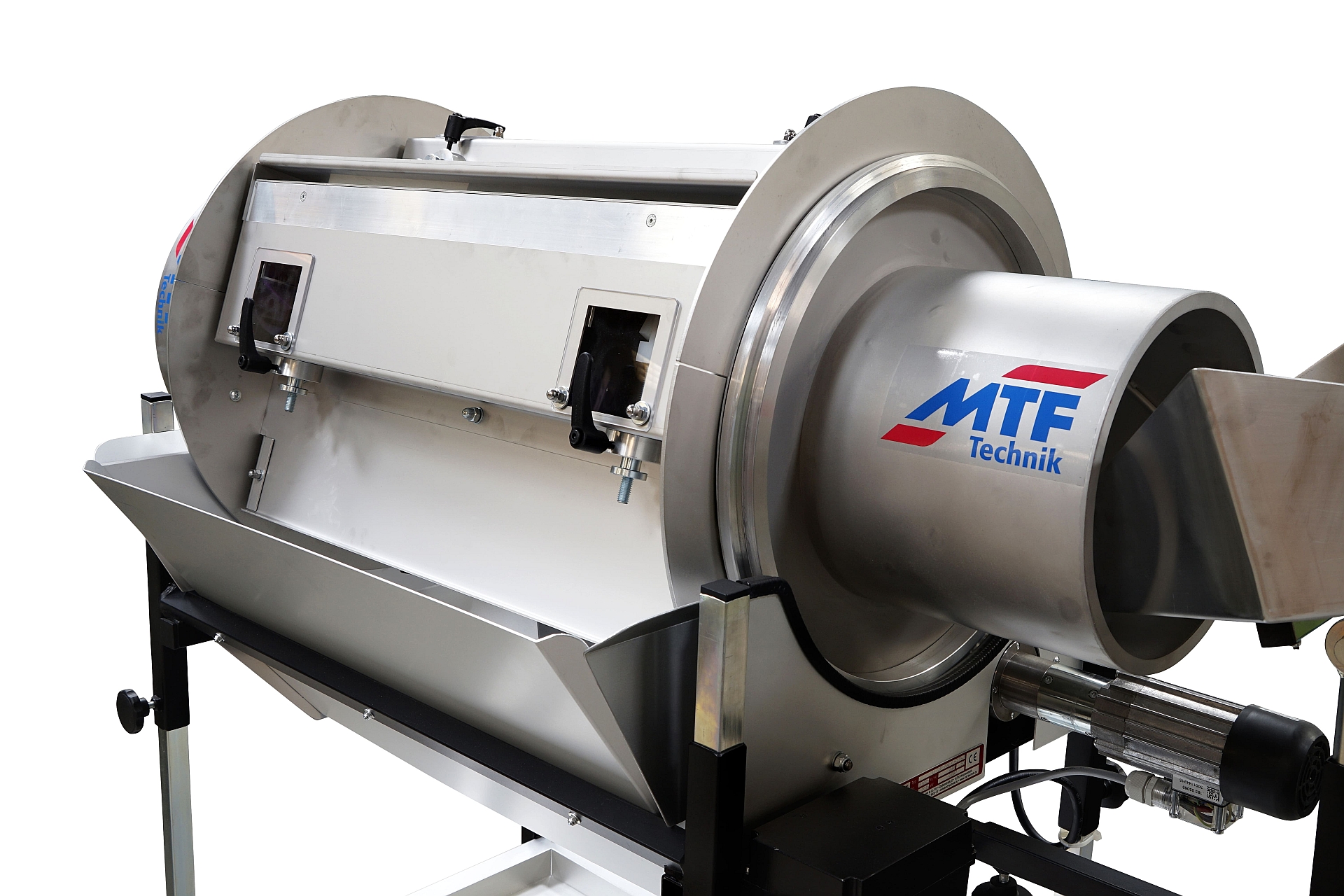
Rectangle Separation Drums
The Rectangle Separation Drums are a completely separate type of separation drum and are usually used for very complex part geometries or soft materials. The Rectangle Drums have four separating gaps, each consisting of two 80 mm wide parallel surfaces. The drum cage is made entirely of stainless steel, meaning that these drums are also used in the production of medical technology items or clean room production, for example. The smooth surfaces are very easy to clean.
As with roller separator drums or screw separators, the separation is also carried out via the height of the components. In addition, the surface-parallel design of the separating gap also prevents components from "wriggling through".
The separating gap of the Rectangle Drum is adjusted using threaded spindles. The height of the separating gap can be precisely adjusted and read by means of applied scales. This ensures a high level of repeat accuracy.
Another key feature of the Rectangle Drum is MTF Technik's patented process of separating gaps that open with each rotation. A special mechanism causes the separating gaps to open briefly in the upper area. This means that components that could get jammed in other drums, such as very small or pointed components, can also be separated in the rectangle drums. Moreover, very soft materials (e.g. rubber or silicone) can also be processed very well in this type of drum.
Do you have further questions? We are at your disposal via telephone via +49 2261 9431-0 or info@mtf-technik.de or please use our contact form.